Fused Deposition Modeling //
FDM 3D Printing
- Prototyping and Production with Thermoplastic Materials
- Unrivaled Toughness for Demanding Applications
- Parts As Soon As 3 Days
Get a Quote
Or Any of Our 25+ Manufacturing Processes
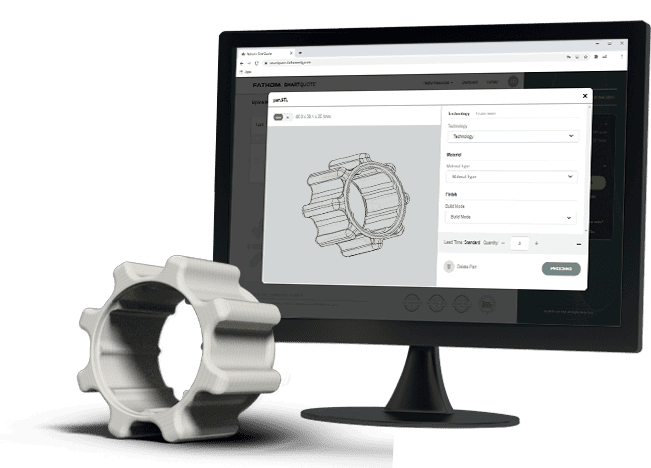
Additive Parts for Your Toughest Needs
with Fused Deposition Modeling (FDM)
Are you seeking an additive technology that can help you validate your part designs for fit, finish and functionality – and produce production parts? Do you wish that these parts could also withstand a variety of extreme environments?
Fused Deposition Modeling (FDM) is a versatile technology, useful for rapid prototyping, part validation and low-volume production needs, using the same thermoplastic materials you use for injection molding. Fathom’s FDM printing service has the capacity and expertise to help you produce high-quality parts to meet your needs.
FDM Parts in as Soon as 3 Days // Get A Quote
How Does FDM Manufacturing Work?
FDM is a filament-based additive technology. Material is distributed by a moving print head that extrudes a heated thermoplastic in a pattern, layer-by-layer, onto a build platform. This technology includes the use of a second material to create support structures that can be dissolved or physically removed after the build has been completed.
FDM thermoplastic parts are strong, durable, and dimensionally stable.
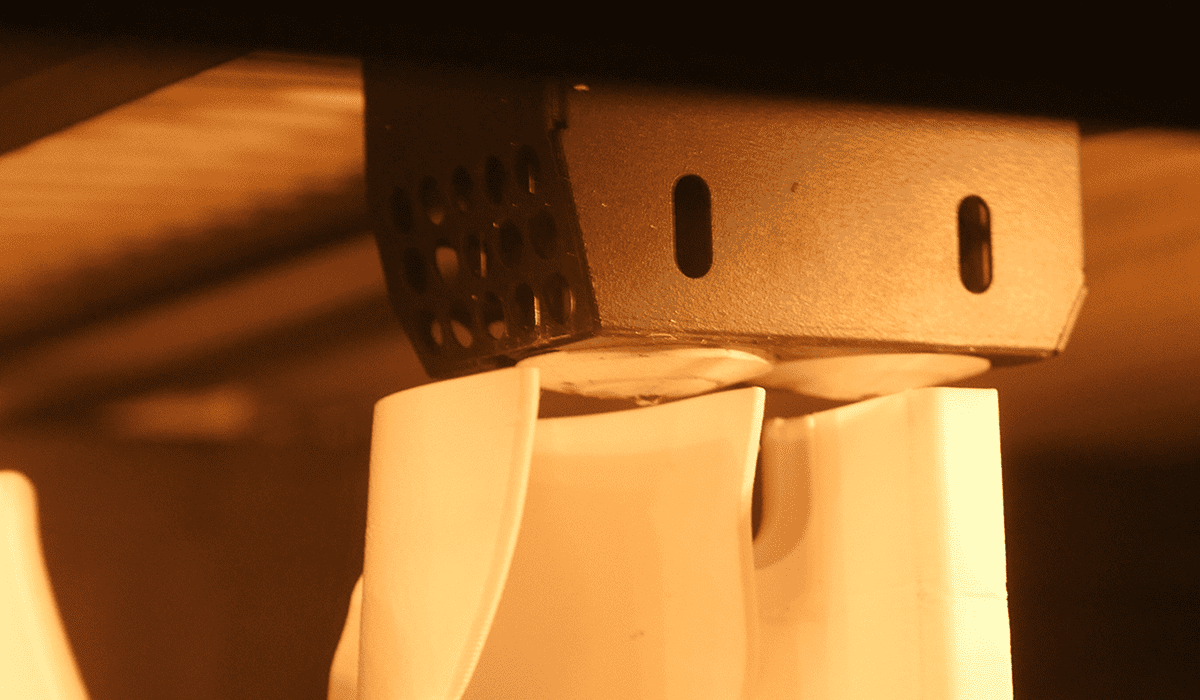
Applications of FDM
FDM parts are durable, chemical resistant and can endure extreme conditions, making them ideal for prototype testing and end-use parts. As FDM manufacturing technology continues to advance, more and more industries are adopting this technology, including:
- Automotive
- Aerospace
- Architecture
- Medical and dental
- Pharmaceutical
- Health and beauty

What Does FDM 3D Printing Make Possible?
FDM parts tend to be tougher and more robust than many other additive technologies, making them equally well-suited for prototyping and production applications. A wide range of engineering-grade thermoplastic materials is available from Fathom’s FDM printing service, including high-performance polycarbonate and high-heat deflection resins.
FDM additive manufacturing can even be used to quickly build jigs and work-holding fixtures. This gives customers the flexibility to take on new projects while lowering their costs. No more waiting weeks or months to have custom fixtures machined to meet their needs.
FDM manufacturing enables the production of larger parts than many 3D printing technologies. This means there is less need to section and post-bond parts to achieve the sizes you need.
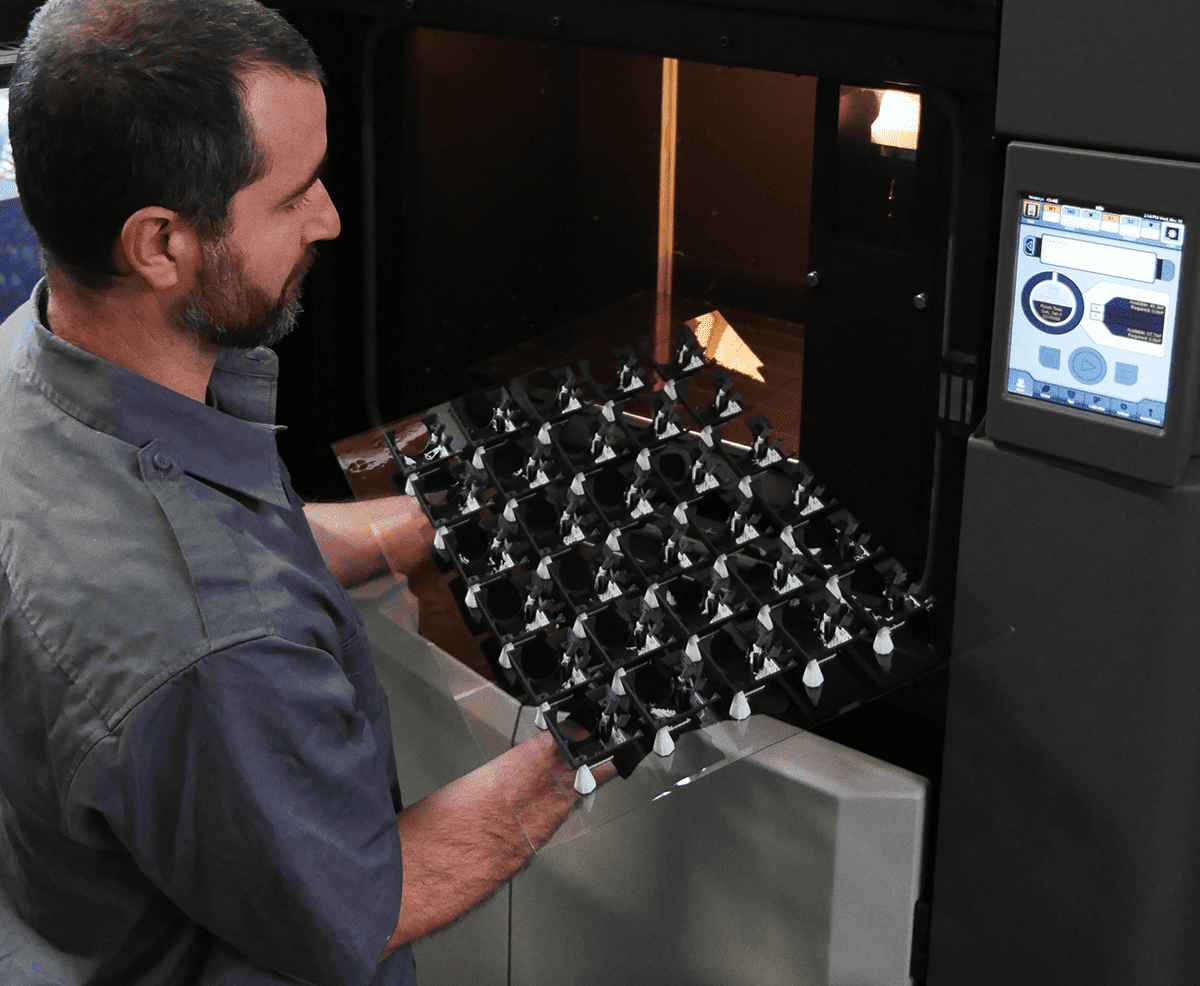
Advantages
A Wide Range of Materials // FDM technology can be used with acrylonitrile butadiene styrene (ABS) polymers, polycarbonates, polycaprolactone, polyphenyl sulfones and more. What’s significant is that FDM can print parts using many of the same materials used in injection molding.
Exceptional Toughness // FDM parts are rugged and durable, ideal for more demanding applications like jigs and work-holding fixtures.
The Same Material, from Prototype to Production // Engineers can print parts to test fit, finish and functionality using the same material that will be used to injection mold production parts.
Build Functional Prototypes Fast // Your FDM printing service can be used to produce functional prototypes within a few hours or days, depending on the complexity of the part. This can help you reduce your time to market.
Support for Low-Volume Production // FDM manufacturing isn’t just for making prototype parts. It also supports low-volume production of parts.
Variable Infill Density // Like many additive technologies, printing large thick areas or bodies can be a challenge. With FDM additive manufacturing, these areas can be filled with customizable lattice structures to speed up print time while still offering a suitable combination of strength and build success.
Disadvantages
Anisotropic Characteristics // FDM parts can be less strong in the Z direction.
Not Ideal for Small Parts or Details // With a minimum nozzle size of 0.4 inches, FDM isn’t well-suited to print small parts or larger parts with tiny details.
Surface Finish // Because the material is extruded in layers, the resulting surface finish tends to be lower fidelity than some other additive methods. That means FDM parts may require more post-processing to achieve a desirable surface finish. Be sure to ask your commercial 3d printing service about finishing options for FDM.
What Can FDM be Paired With?
FDM parts can be post-machined to meet specific tolerances. They can also be bonded to other assemblies, such as fiberglass panels and other additive parts. They can also accommodate a variety of post-installable hardware and inserts.
Traditional Technologies That Can Benefit from FDM
If you’re currently using CNC machining, injection molding or other traditional methods to produce prototype parts, FDM may be a faster and more flexible alternative.
FDM manufacturing can be used to produce low-production runs of thermoplastic parts, ideal for bridge production or while you’re waiting for conventional manufacturing tooling to be completed.
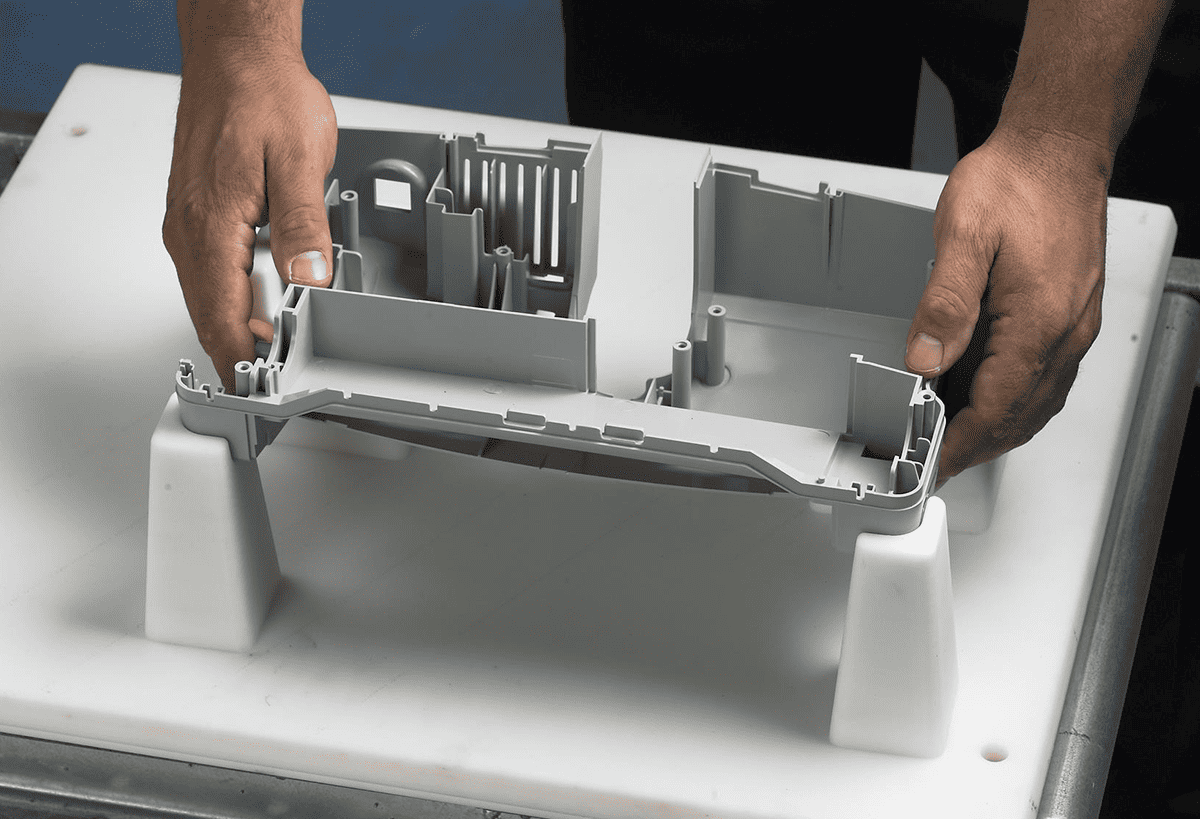
FDM Materials Available
Fathom’s FDM printing service can print parts using a variety of high-performance engineering thermoplastics, including ABS, polycarbonate (PC) and Ultem.
Not sure what you need? Talk to a Fathom expert today!
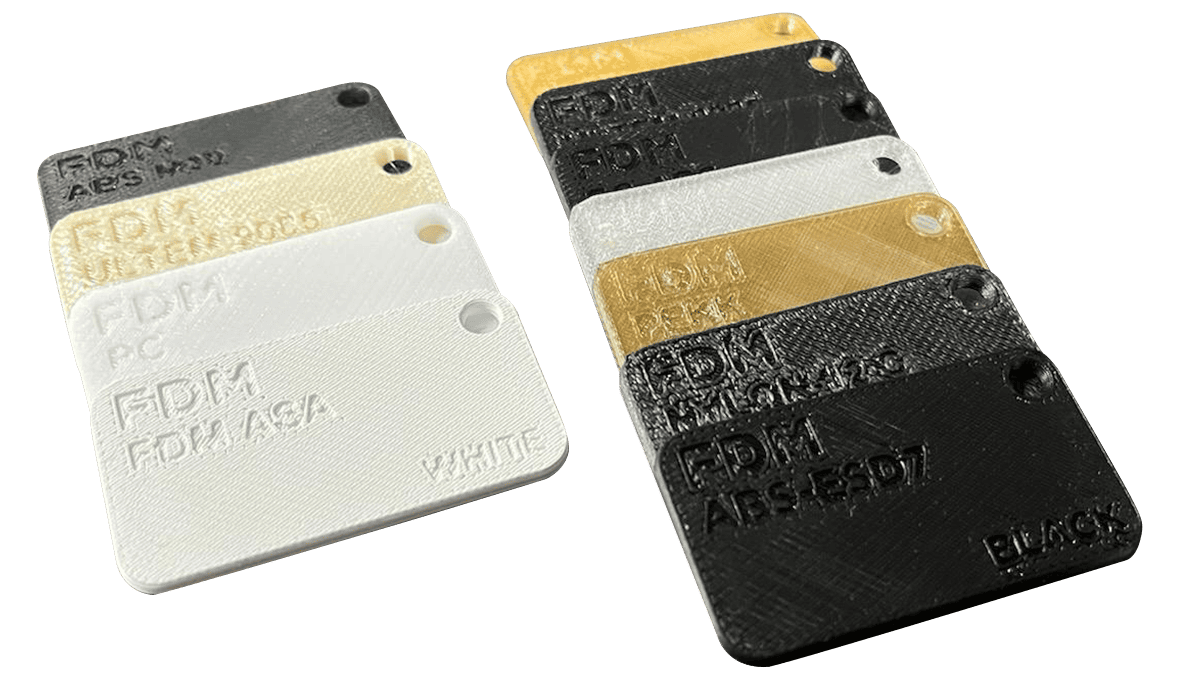
Finishing Options for FDM Parts
Fathom offers these post-processing services for FDM printing service:
- Sanded
- Tumbled
- Media blasted
- Vapor smoothed
- Painted (EMI shield)
- Painted (sand and paint, non-cosmetic)
- Painted (sand and paint, cosmetic)
- Painted (customer spec paint)
- Specialty coated
- Plated
- Decals
- Pad printed
- Screen printed
- Inserts
- Post-machined
- Assembly
Our craftspeople are ready to meet your post-processing needs. Talk to an expert now.
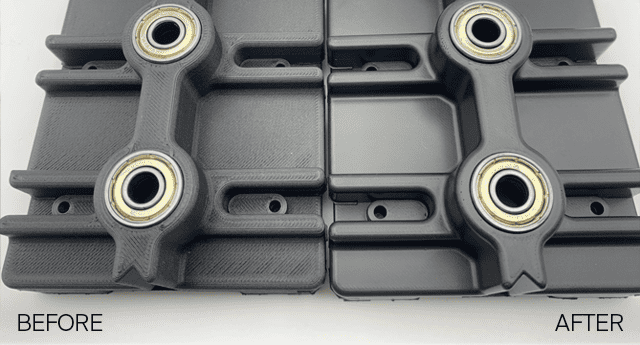
Vapor Smoothing
Fathom offers AMT’s PostPro3D technology, a smart and automated post-processing solution for smoothing FDM printed parts. PostPro3D can achieve a high-quality surface finish that matches injection molding techniques when using 3D printing processes.
Why Choose FDM 3D Printing?
Material Characteristics
If you need thermoplastic parts that are strong, durable, and dimensionally stable, FDM additive manufacturing is an excellent choice.
Performance
FDM offers a wide range of materials with performance characteristics that meet many high-performance needs, including heat, chemical, impact, fatigue resistance and biocompatibility.
Prototype to Production
FDM manufacturing is suitable for both prototyping and case-by-case production runs, and provides a closer approximation to end-use production manufacturing methods because it utilizes the same thermoplastic-grade materials.
Size Capacity
If you need to build larger parts, Fathom’s FDM printing service offers one of the largest build sizes of any additive technology.
Why Choose Fathom’s FDM 3D Printing?
Fathom has the expertise and technology to help you meet your needs faster.
Fathom’s FDM printing service has the capacity and knowledge to help you produce high-quality FDM parts to meet your prototyping and production needs. An experienced engineer will help you first determine if FDM manufacturing is the right solution for your needs and will then help you optimize your part design for the best results.
Get a quote on your FDM project today with our SmartQuote platform.