Energy & Renewable Energy Manufacturing
Renewable energy has become one of the fastest-growing industries in the world, as startups and large companies seek new ways to generate sustainable sources of energy. Modern digital manufacturing methods are the linchpins that make renewable energy practical, including: Solar, Geothermal, Wind, Hydropower and Biomass.
How Can Fathom Help You with Your Energy & Renewable Energy Manufacturing Needs?
We can…
- Provide you with engineering assistance to help you optimize your designs for manufacturability, reliability and longevity.
- Help you select the best materials for each component to help ensure it provides optimal performance and longevity in your critical applications.
- Support you throughout the product life cycle – from rapid prototyping of new part designs through bridge and production manufacturing.
- Help you manage your supply chain for service and replacement parts.
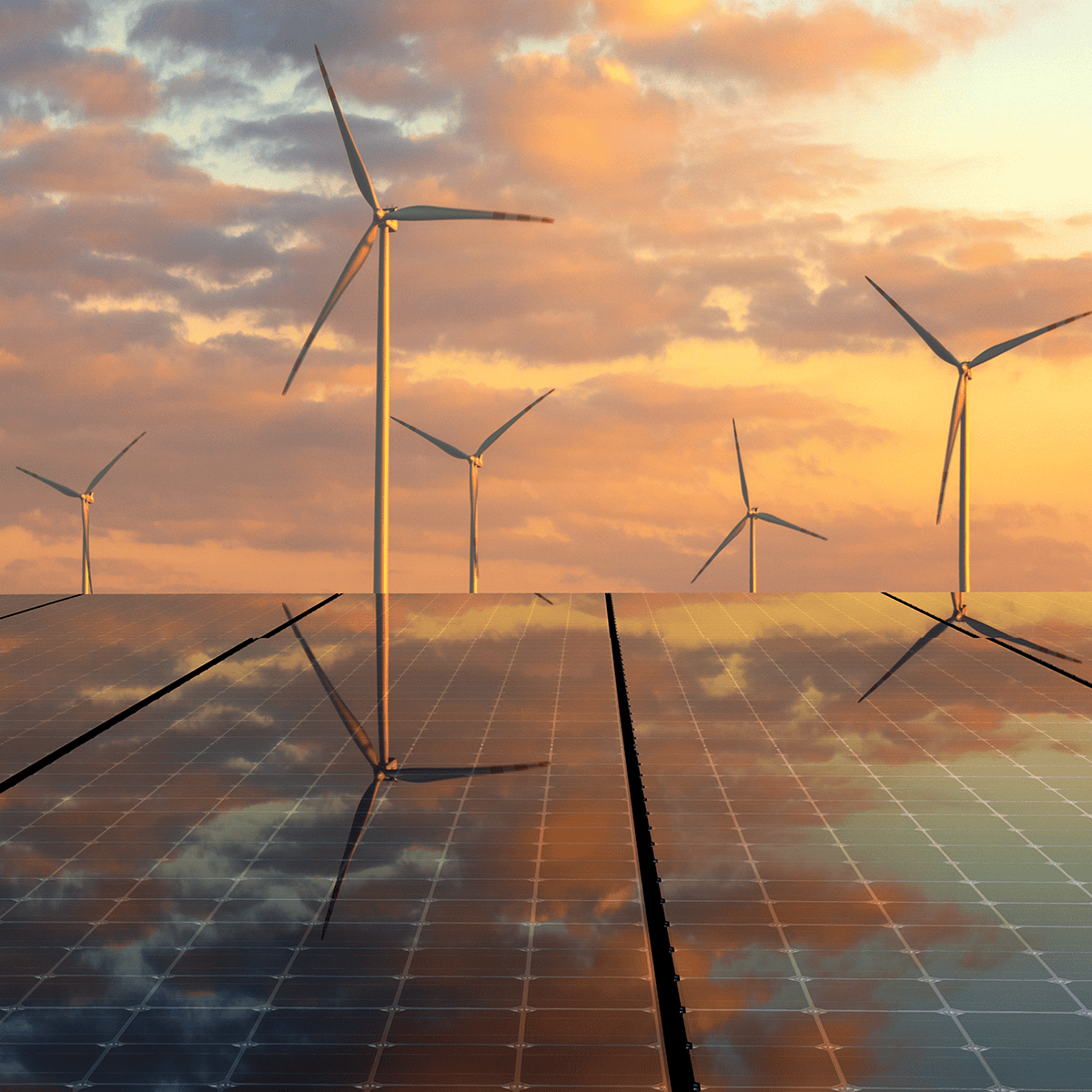
Technologies for the
Energy & Renewable Energy Manufacturing
Sheet Metal Fabrication
Sheet metal fabrication is used to form a variety of components for renewable energy systems for solar, wind and geothermal applications. Typical parts include frames, brackets, connectors, housings and enclosures.
Fathom can fabricate both small, complex parts such as brackets and fixtures and large structures like housings and enclosures. Rapid prototyping can be used to validate part designs and bring them to market faster.
We can also produce extremely flat, burr-free washers, shims and spacers using a unique fabrication technique called photochemical etching.
CNC Machining
CNC machining is used to produce high-quality parts for renewable energy systems, such as turbines, rotors, gears and bushings. Fathom offers decades of experience in milling, turning and grinding to produce reliable precision parts. Reliability is especially important to this industry because most power generation and distribution equipment is located in remote areas.
Additive Manufacturing
Additive manufacturing holds the key to accelerating the adoption of renewable energy. It enables companies to streamline and accelerate new product development through rapid prototyping. Here are a few examples:
- Engineers can develop part designs that aren’t possible using subtractive manufacturing techniques, such as internal cooling channels and the ability to replace thick walls with weight-saving lattice structures.
- Designs can be quickly refined and customized using rapid prototyping techniques.
- Assemblies can be simplified into single parts.
- Many types of parts can be produced without tooling, accelerating their time to market.
In addition, most renewable energy additive manufacturing techniques make very efficient use of material, with little or no waste.
Fathom can produce rugged plastic parts using additive technologies like Fused Deposition Modeling (FDM), Selective Laser Sintering (SLS) and Multi Jet Fusion (MJF). Additive metal technology, such as Direct Metal Laser Sintering (DMLS), is an ideal fit for more demanding applications.
Fathom offers decades of expertise helping its customers optimize their part designs for additive manufacturing and select the materials and manufacturing methods that will meet their requirements. Our rapid prototyping services can help you validate your designs and bring them to market faster. We also provide a full range of post-processing services to ensure that your parts produced using renewable energy additive manufacturing methods will meet all your cosmetic and functional requirements.
Injection Molding
Injection molding is used to make a variety of parts for renewable energy systems, including wind, hydropower, solar, biomass and geothermal applications. It’s also used to fabricate battery racks and enclosures for energy storage systems.
Fathom offers both domestic and overseas injection molding solutions to meet a variety of needs and price points.
Energy & Renewable Energy Applications
Fathom parts used in energy and renewable energy systems include:
Sheet Metal Fabrication
- Frames, posts, brackets and enclosures for solar arrays
- Turbines
- Heat exchangers
CNC Machining
- Solar panels, frames and rails
- Bearings
- Rotors
- Gears
- Shafts
- Bushings
- Turbines
Injection Molding
- Blades
- Valves
- Turbines
- Flanges
- Pumps
- Motors
Additive Manufacturing
- Gears
- Fixtures
- Shafts
- Turbine blades
- Impellers
- Rotors and stators
Quality is Fathom’s Number One Priority
At Fathom, our commitment to in-house inspections enables us to turn around parts quickly, including CMM validation, surface inspections and tensile strength testing.
In addition, we have a proven ability to comply with customer-specific process, material and workmanship standards.
Certifications
Visit our detailed list of Fathom certifications to view registrations held by each of our sites.
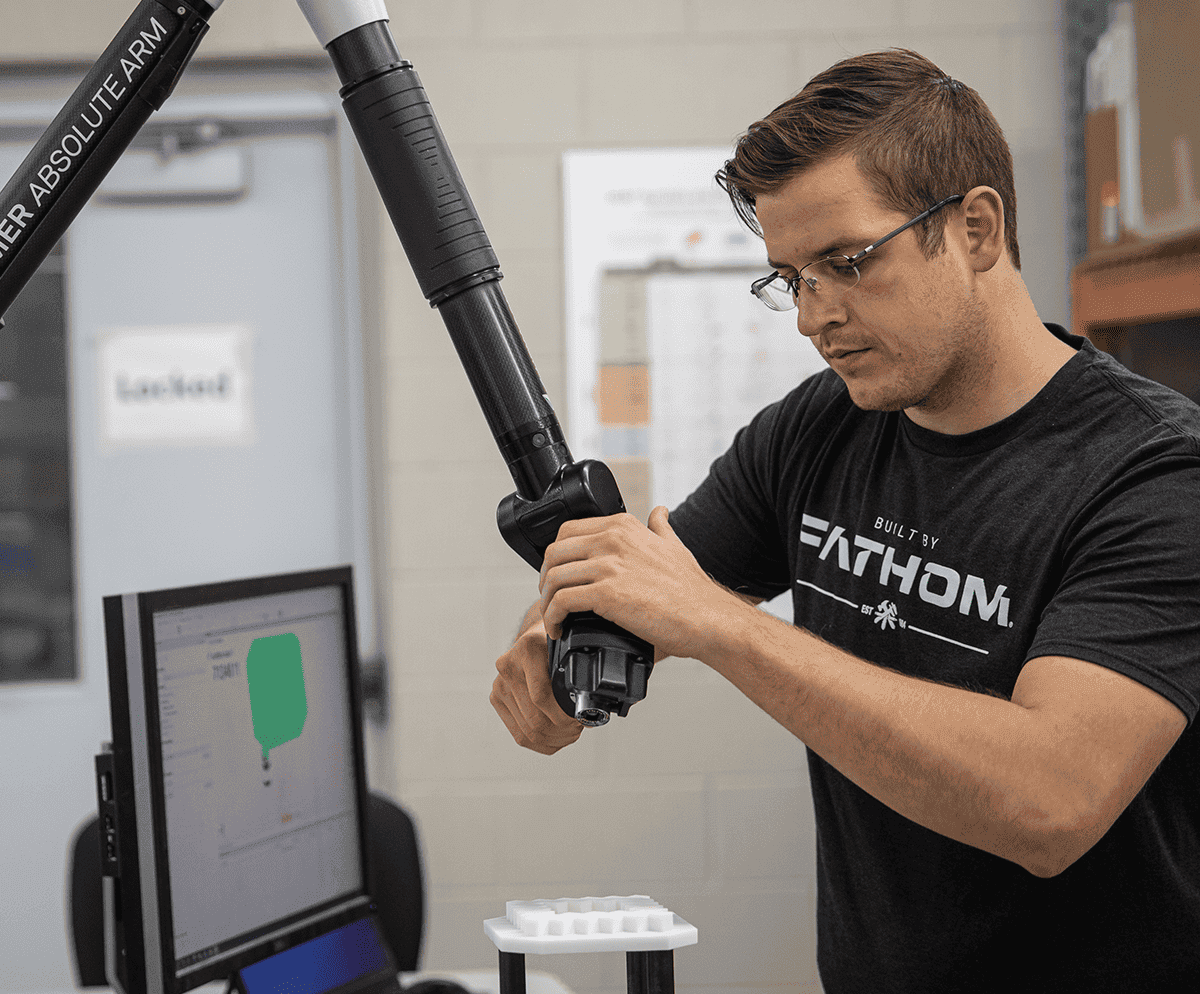
Why Choose Fathom?
- We have the systems, processes and technical expertise to be able to deliver short-run, highly customized parts for your energy and renewable energy applications that meet your requirements.
- We’re focused on new product innovation, rapid prototyping and bridge/short-run production. We can match your speed and agility.
- We can support your needs throughout the product development lifecycle – from early prototypes for design validation and late-stage prototypes to verify fit, finish and functionality as well as bridge production and full production.
- We offer an unmatched breadth of manufacturing technologies – in-house, not via third parties – to meet all your needs, including renewable energy additive manufacturing, precision CNC machining, sheet metal forming and injection molding.
- We’re problem solvers. Bring us your complex geometries, short-run/high-mix parts and “impossible” projects. We’ll help you get the work done!