3D Printing for American Decathlete
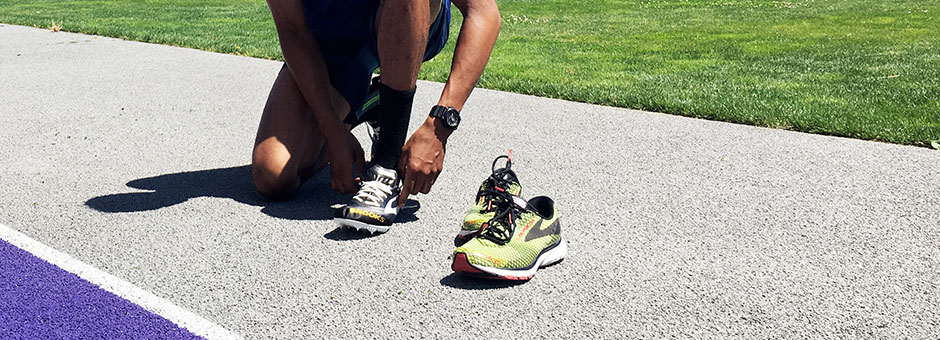
Brooks Running and Fathom came together this summer to prototype a pair of personalized sprinting shoes featuring 3D printed spike plates for American decathlete Jeremy Taiwo—check out the coverage from NBC Bay Area below. By working with the latest technologies from advanced manufacturers like Fathom and engaging with professional athletes during the iterative design process, Brooks is grounding its innovation efforts where foot meets track. This style of shoe isn’t available in stores yet because Brooks is deep in the product development process, getting real feedback from real athletes like Taiwo and other Brooks-sponsored runners who often push themselves and their gear, to the limits.
REAL ATHLETES, REAL FEEDBACK
Built to Taiwo’s exact specifications at the Brooks manufacturing facility using additively manufactured spike plates by Fathom, the shoes were rigorously tested during a product feedback session just days before the decathlete made his mark at a highly anticipated event.
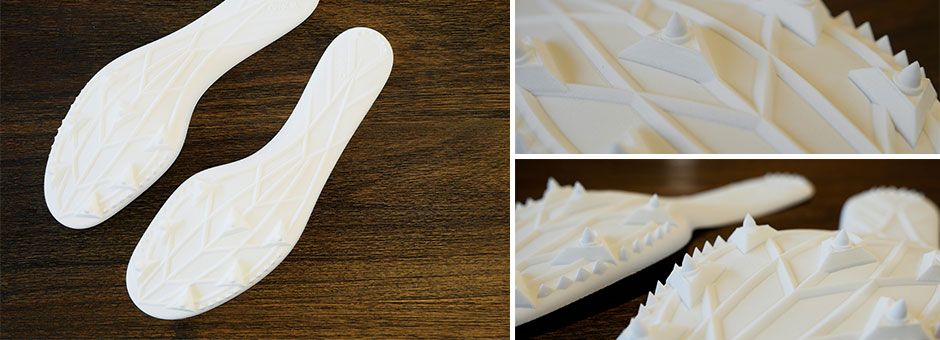
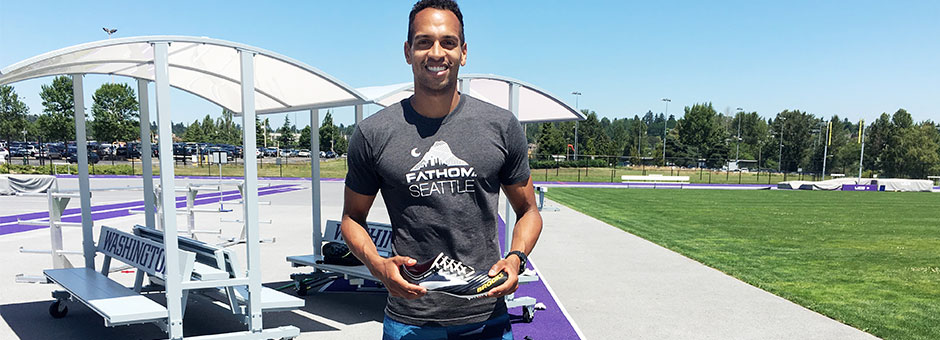
3D PRINTING FOR FOOTWEAR
Creating a spike plate with the correct flex, stiffness and rebound are critical to a fast start and sustained speed for a track and field athlete, especially a decathlete. In order to test a design, shoe manufacturers would traditionally rely on injection or compression molded parts—a process which takes a long time to prep and produce. Just getting from concept to prototypes to manufactured parts can take up months, especially if there are design changes that affect the production tools.
By leveraging a blended approach, using 3D printing early on in development and all the way through production, teams are drastically compressing product development timelines and reducing total cost of ownership—companies like Brooks are making products better and faster for its customers.
Brooks, for example, was able to use functional and testable prototypes made in a durable Nylon material to survive real-world product testing (SLS or Selective Laser Sintering, was the additive technology chosen for this application). This actionable insight, collected both qualitatively from athletes like Taiwo and quantitatively though pressure sensors, provide designers and engineers with significant data sets that can be used to adjust the design for the best performance.
INDUSTRY REALITY VERSUS HYPE
Although there is a lot hype about 3D printing changing the way footwear is made in the future of the consumer shoe industry, there are many immediate and practical ways that today’s technologies are already improving the performance of traditionally manufactured goods. This additive manufacturing example from Brooks, improving performance for professional athletes and running enthusiasts, is one of many examples that remind us that 3D printing has a meaningful and measurable impact on product development.
The shoe industry at large has been making headlines for interesting uses of 3D printing for years. The practice is becoming increasingly commonplace as technologies, materials and software further develop. Wired writer Margaret Rhodes recently covered Nikes use of 3D printed spike plates made using generative design and last year writer Edgar Alvarez of Engadget wrote about Adidas for showing how 3D printing could be used to make midsoles for running shoes. 3D printing is popular in the high fashion scene, too, with designers using these advanced methods to create unique works of art like Molecule heels by designer Francis Bitonti on display at the Museum of Fine Art in Boston.
IN THE NEWS
Scott Budman of NBC Bay Area recently covered the story in a news segment.
Fathom & Brooks Running Are Not Official Sponsors of the Olympic Games