Design Differently Model of the Month
Congratulations to Carlo Quiñonez, Fathom’s Director of Research, whose 3D printed Aquino Thermal Chamber was chosen as Design Differently’s Model of the Month for May! To elaborate on the innovative functionality and inspiration behind this model, Quiñonez shares his thoughts on complex geometries, designing for additive manufacturing and open-source ideals. Stay tuned for more because the team has something special planned for this design. Check back soon!
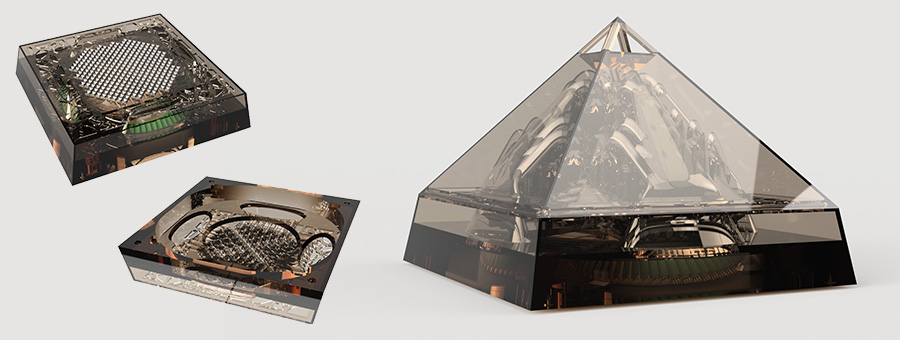
Most incubators utilize metal plates to maintain a constant temperature — how does your 3D printed thermal chamber function using only plastics?
Quiñonez: Metals are used because of their inherent thermal conductivity, which allows engineers to use a small heating element like a burner or electrical heater without worrying too much about hot spots because the metal will spread the heat evenly. This approach wouldn’t work with insulators such as plastic. A focused source of heat on plastic would cause the temperature to increase quickly and subsequently melt the plastic.
To heat plastic, you need to overcome several challenges:
-
Diffusion. You need to apply heat using very low watts per surface area. We accomplish this by using hot air to warm the plastic.
-
Even heating. The hot air must be piped throughout the structure so that all areas receive the same amount of heating.
-
Heat transfer. Since plastic is an insulator, it doesn’t allow heat to move very quickly. We have specially designed heat exchangers that extract the heat from the air as close as possible to the interior surface of the chamber.

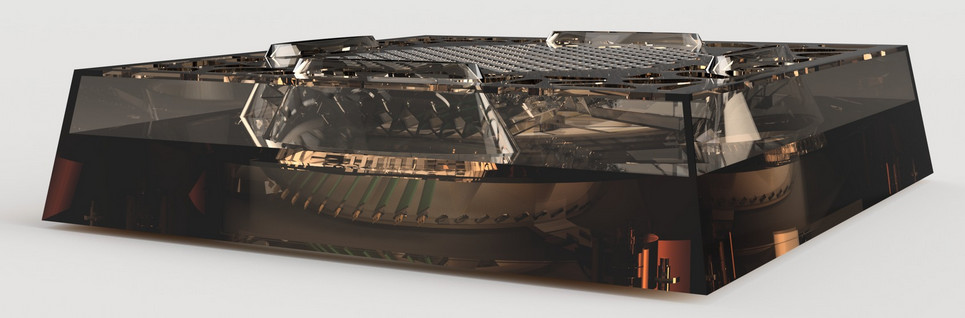
Normally, these types of tight clearances and thin walls would require delicate and time-consuming support removal — how did you leverage complex geometries to your advantage to avoid this labor-intensive process?
Quiñonez: Designing all the geometry to be self-supporting was a cardinal constraint. This is what Design for Additive Manufacturing (DFAM) is all about. In conventional design projects, someone with manufacturing experience looks over designs and says, “We can’t injection mold this,” or, “If we changed this, it would be a lot easier to machine.” Basically, they’re optimizing the design for conventional manufacturing. I think the engineering community needs to start embracing DFAM. In the thermal chamber, I kept iterating on the design to eliminate supports. Since sloping sides of 45 degrees are self-supporting on FDM printers, I focused on the pyramid shape for the chamber.
Prior to joining Fathom, you earned a doctorate in biology and served as a post-doctoral researcher at the University of California, San Diego — how has your extensive background in life sciences contributed to this project?
Quiñonez: Science taught me to always question assumptions. Engineering is all about minimizing risk and the simple way to do that is by doing things the same way that have worked previously. Studying science definitely saved me from learning the “right” way of making things.
I was also exposed to all of the wonderful hardware scientists create in their labs. Because science focuses on new and unknown phenomena, commercially available tools and instruments often require modification and customization so they can be used in a given experiment. A lot of big advances in science were driven by new tools and capabilities. What I’ve realized is that scientists are already Makers.
It often takes years of experience and experimenting to develop truly innovative solutions — tell us about the evolution of your work on the thermal chamber project.
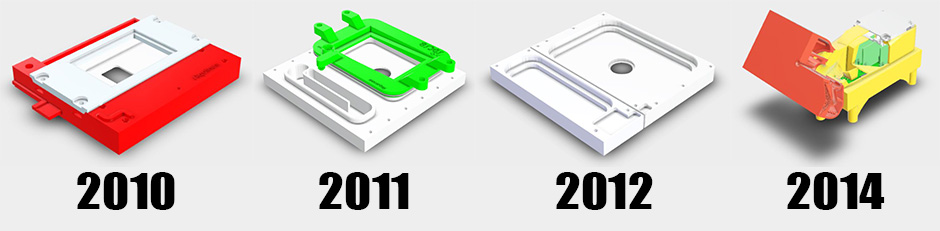
Quiñonez: This was part of a project I started in 2009 when I was a post-doctoral researcher at UCSD. I was rebuilding an instrument constructed by graduate student as part of his thesis. A key component was the incubator; a thermal chamber with some specialized features for growing cells in petri dishes. When I recreated the instrument, I focused on using 3D printing to make it easier for other scientists to develop their own versions. The design of the incubator went through many revisions. At first it looked a lot like the commercially available units, but over time it evolved to reflect the design freedom of 3D printing. However, all of the versions I made previously featured a metal chamber and only used 3D printing for the plastic parts of the incubator. It wasn’t until recently that I thought about eliminating the metal chamber and replacing it with plastic.
As you mentioned, lab equipment can be expensive and difficult to customize or modify — how does your 3D printed incubation chamber address these obstacles?
Quiñonez: 3D-printable designs are basically self-documenting. This means that if you’ve printed something out, then you also made the CAD file that documents everything you printed. It’s easier to share and lets other people start where you left off if they want to improve or further modify the design. Also, if you’re using a service bureau, the cost of 3D printed equipment compares favorably with the cost of conventional instruments. If you have a 3D printer, the cost of 3D printed equipment is almost negligible; you’re just paying for the material.
It’s apparent in your work that you are continually capitalizing on the unlimited design freedom of additive manufacturing — what are some other projects to which you’re currently applying this mentality?
Quiñonez: I’m currently working on a stepper motor, tensegrity structural components, positioning systems and sensors—all 3D-printable. These design embody CAP, a new engineering mentality that needs to replace KISS. This common acronym, stands for Keep It Simple Stupid and it’s the first thing that’s drilled into the heads of engineering students. CAP is the new acronym for the additive age: Complex As Practical. If you want to leverage the strengths of 3D printing, you have to make your parts as Complex As Practical. All of the designs I’m working on embody CAP.
To read more about the development of the Aquino Thermal Chamber, check out the Design Differently post on this winning design.