Composite Tooling Design: Guide to Materials & Manufacturers
Last year, the team at Stratasys launched an FDM-focused composite tooling design guide so its machine users could more confidently design, build and use the enterprise-level additive technology of composite tooling manufacturers. Due to the popularity of the design guide, Stratasys released a 2nd edition with 99 pages of useful information. → Download Today / / Composite Tooling Design Guide for FDM 2.0
So, What’s New In The Latest Version of The Composite Tooling Design Guide?
NO. 1 / / Updated Best Practices—Although there are many ways to approach the various challenges that can arise when creating composite tool designs for fabrication, the updated digital book includes recommendations for many common scenarios Stratasys experts have encountered to help ensure your success. Specifically, the guide includes updated best practices for //
-
Scribe Lines
-
Tool Repair
-
Incorporating Localized Reinforcement for Inserts
-
Near-Net-Shape Tooling (Machining FDM Tools)
-
Multi-Section Tools
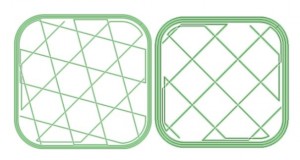
NO. 2 / / More Data—The design guide includes test data for ULTEM 1010 at critical cure temperatures, as well as empirical data for pressure resistance of the new hexagram fill pattern.
The hexagram fill pattern has shown the potential to reduce composite tooling material use by 200% compared to the more traditional sparse double dense fill pattern (views of the Insight-generated fill patterns—hexagram on the left and sparse double dense on the right).
NO. 3 / / New Case Studies—The design guide includes new customer case studies from Dassault Falcon Jet, Rock West Composites and Team Penske to illustrate how different industries are leveraging FDM technology to ease the manufacturing and procurement process, allow for rapid response to customer needs and accelerate innovation.
About the Digital Book
Reduce the time and cost to produce composite structures by using tools made with enterprise-level FDM Technology instead of traditional methods. Taking this approach to composite tooling enables cost-effective prototyping and simplifies tool design and fabrication while increasing functionality. It can reduce lead-time from months to days and reduce tooling costs by more than 50%.
In this design guide, you’ll learn—how to choose the appropriate FDM material based on your design criteria, how to design tools using the most effective methods of construction, how to process the CAD file for optimal build results and how to post-process tools to achieve the best composite fabrication outcomes. The design guide also includes multiple use-case and customer examples of FDM composite tooling applications.
Want to talk to an additive technology expert? Fill out the form (top of page) to start a conversation with us today!