Doblet Goes From 3D Printing to Injection Molding
Doblet Goes From 3D Printing to Injection Molding—Faster Iterations and Better Development For This Growing San Francisco Bay Area Company
Doblet is the world’s first network of batteries on demand for charging phones everywhere. The company’s mission is to provide portable power anywhere consumers happen to be. Using patent-pending technology and the Doblet mobile app on iOS or Android devices, users are instantly notified of the nearest place to pick up a charge the moment their batteries start to run low.
In developing the product, Doblet faced a number of challenges endemic to hardware startups and utilized a range of Fathom’s advanced manufacturing services throughout their product development process. Fathom sat down with Co-Founder Jeff Chang to discuss Doblet, the startup struggle and 3D printing.
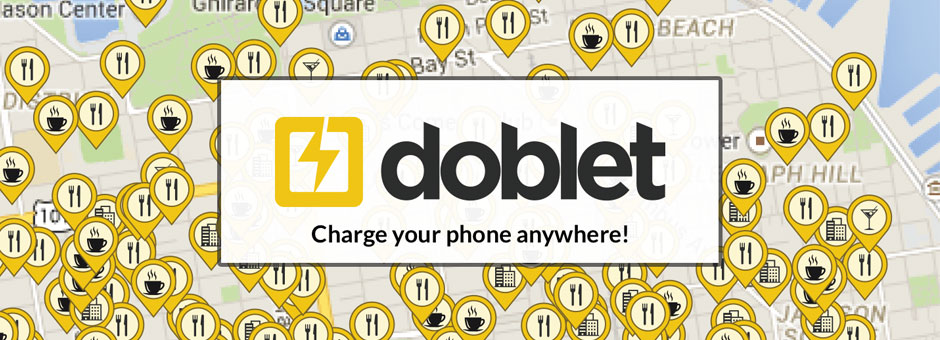
Fathom consistently works with companies that view common problems as challenges and look for creative fixes. What is the story behind Doblet?
Jeff Chang—Doblet solves the phone battery problem.
We’re building a network of smart portable batteries, so you can charge your phone anywhere. We put our batteries in bars, restaurants, coffee shops, gyms, hotels, libraries, museums, co-working spaces and all sorts of other venues. When you run low on charge, just pick up a Doblet, charge your phone, then drop the Doblet back off.
Doktor, my co-founder, was at a bar in San Francisco, charging his phone with an external battery. The guy next to him asks, “Mind if I borrow that battery after you’re done? I’ll buy you a beer!” The guy on the other side says, “I’ll buy a beer for both of you, if you can charge my phone too!”
Doktor wondered why charging wasn’t just readily available, right where & when you needed it. And so Doblet was born.
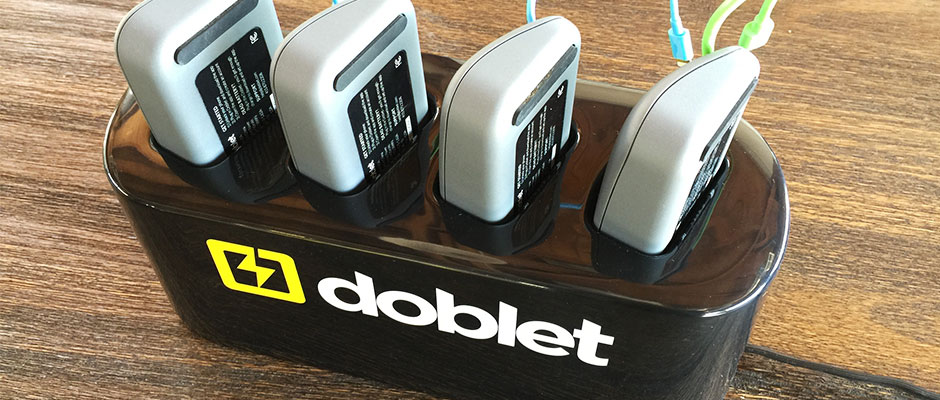
Were there any challenges during development for Doblet that only proved solvable through working with Fathom?
Jeff—Yes; we were facing a tight deadline, with the need for a moderately small production volume (5000-range) on a set of large injection molded parts. Fathom was the best firm we could find, for high-quality injection molding on short notice, who would also provide secondary processes (pad printing, etc.) and shipments directly to our US manufacturers warehouse in Shenzhen.
Did 3D printing allow you to test more prototypes or to speed your product development?
Jeff—Fathom provided excellent-quality high-accuracy 3D printing work during the prototyping stage, matching our need for narrow tolerance ranges on large parts. Having physical prototypes to see, handle and feel are key to any product development cycle.
We used 3D printing at every stage, ranging from multiple prior iterations of Doblet prototypes, to our looks-like fully functional model Doblet from Taiwan, to high-accuracy 3D prints of our recharging bay done by Fathom.
We cant imagine why a popular meeting place wouldnt want to offer convenient, design-centric charging stations for patrons—how many businesses are now enrolled with Doblet? Does the team have plans for further expansion?
Jeff—We’re now live in just over 350 venues across the SF Bay Area, with 1,000+ more venues already pre-signed and waiting for hardware. We’re also signing off on international distribution deals in Europe and Asia and running pilot tests with several large corporate and government partners.
Two new iterations of Doblet hardware are launching over the next year, with many improvements that simplify & streamline the user experience – these will coincide with launches into many more venues both here in the Bay Area and elsewhere and new expansion plans with our corporate partners.
We’re looking forward to trying out 3D printed tooling for the upcoming Doblet V2 hardware!
To learn more about Fathom’s advanced prototype fabrication and low volume production services by way of 3D printing, CNC machining, urethane casting, rapid tooling and injection molding—start a conversation with an account manager today.