Form, Fit, Function Medical Device / / SLA Prototyping
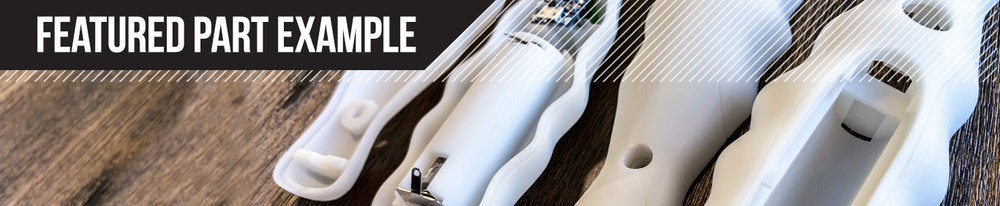
3D Printing & Rapid Prototyping
Handheld Medical Device / / Evaluating Fit-Check & Ergonomics Within One Week
In this featured post, Mechanical Engineer Anne Pauley and Applications Engineering Manager Tony Slavik highlight the practical application of prototyping with 3D printing to test form, fit and function of a part intended for tooling and injection molding.
The Project // Ergonomic Handheld Medical Device
Featured Method Used // Surface Modeling
Featured Software Used // Fusion 360 & Magics
Additive Technologies Featured / / Stereolithography (SLA) & PolyJet
Fathom Teams // Engineering/Design + Applications Engineering
Fathom Designer // Anne Pauley, Mechanical Engineer
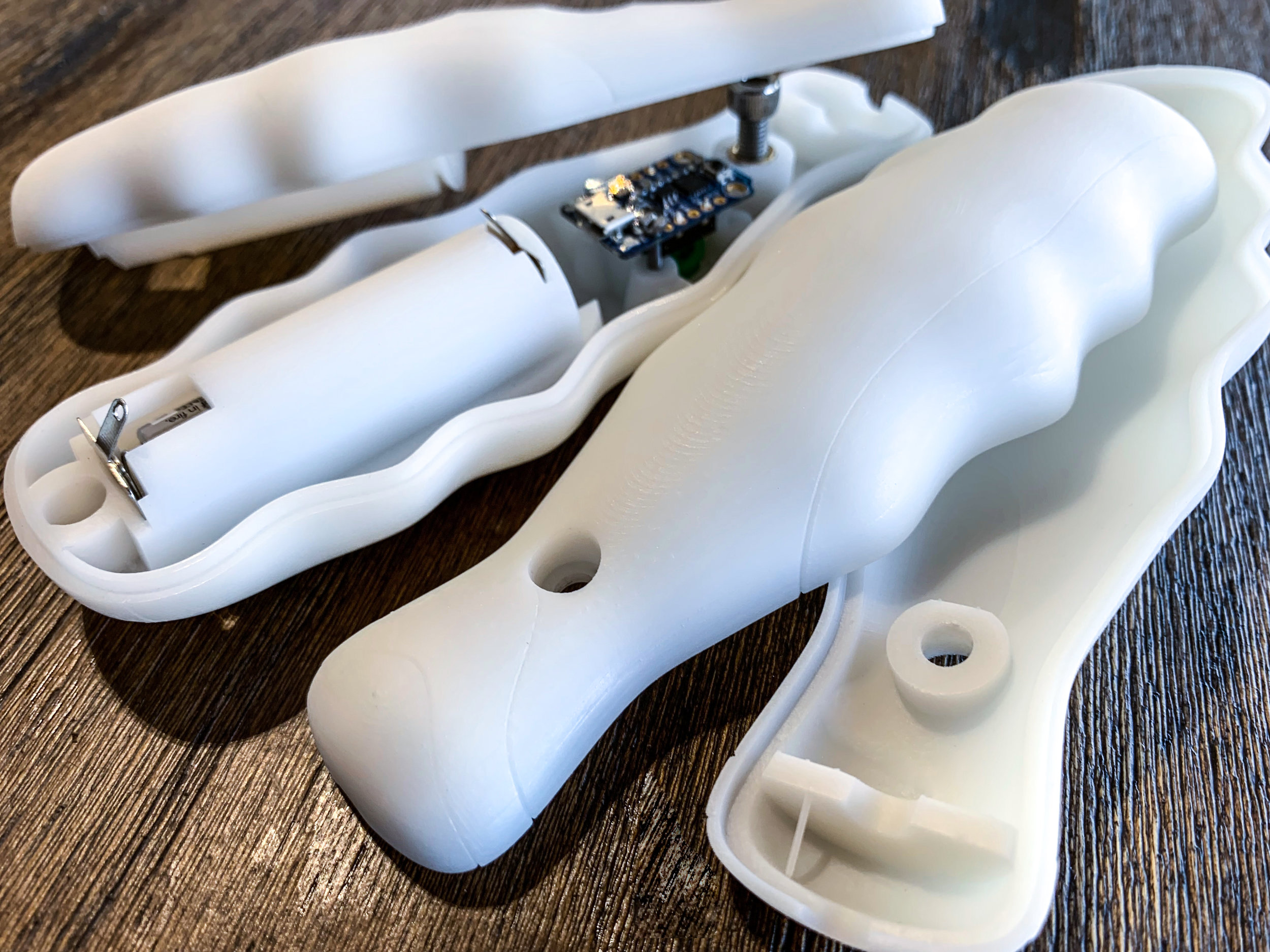
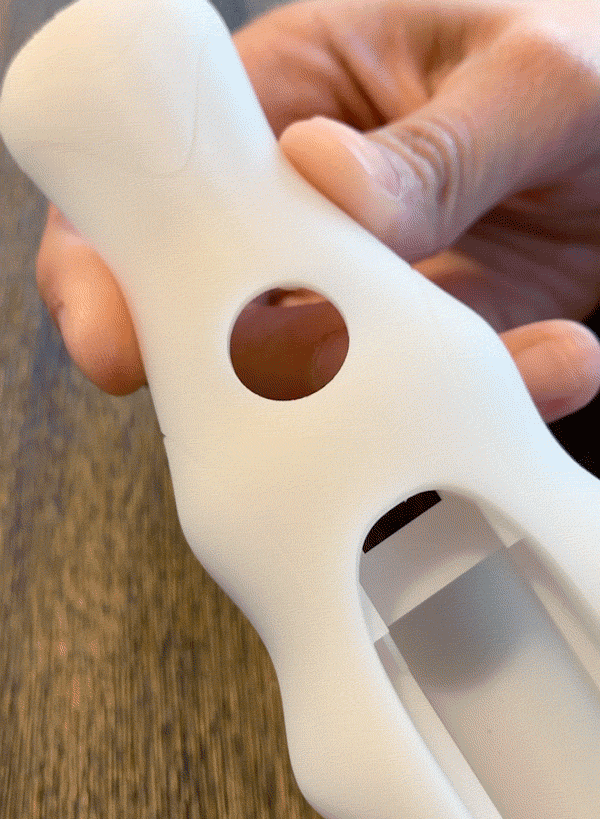
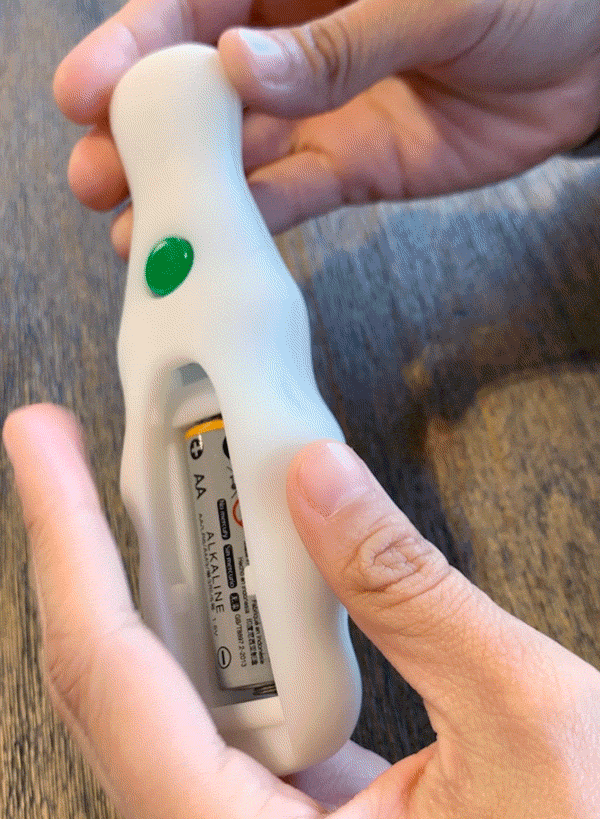
The Part / / T-Spline Ergonomic Medical Handle Device
Mechanical Engineer Anne Pauley on Fathom’s Engineering & Design team designed an ergonomic medical device handle. She included component mounting points because the end goal would be to tool up for injection molding. To design the ergonomic shell, surface modeling in the Fusion 360 t-spline environment was used to easily manipulate surface contours and create a form that is aesthetically pleasing while also functional. The interior structures were modeled to mount a battery, battery contacts, microcontroller and tool mounting.
The Prototype / / 3D Printing to Test Form, Fit and Function
For this prototyping application, the capabilities and benefits of stereolithography (SLA) and PolyJet were considered for testing form, fit and function of the handheld medical device. Typically, SLA is used for med- to large-sized parts, as well as its accuracy and smooth surface finish capabilities. PolyJet is also ideal when aesthetics matter but offers a wider range of rigid and flexible material options, plus it has the unique advantage of multi-material capabilities (e.g. simulating overmolded parts and color).
Based on the application requirements, either technology would achieve a smooth surface finish similar to an injection molded part. Since the design did not include color or required multiple materials, Applications Engineering Manager Tony Slavik advised Anne to try SLA (pictured above). By leveraging this additive technology, she was able to quickly iterate on her design faster at a lower cost than traditional methods. She used the 3D printed prototype to test component mounting, fit check between shells and hardware and ergonomic feel.
Polypropylene is the intended production-grade material, so using Accura 25 for SLA was a natural fit. This material would achieve similar mechanical properties, as well as feel, of the final product. Taking this approach would ensure more accurate feedback for the assembly process and ergonomics.
The Value / / Rapid Prototyping of Entire Design Within One Week
The ability to quickly iterate in this way allowed the engineer to assemble and test the fit of the board, battery and tactile button placement. The accuracy capabilities of SLA makes it possible to evaluate the fit and feel of the button, as well as if the board fits with no interference. Testing this earlier on means the assembly process will be easier and more efficient during the production of the final parts. Since each iteration cost less than $200 and lead-time was within 24 hours from order to delivery, the needed changes were identified, tested, modified and finalized within one week.
Design Guidelines // Fathom’s application and engineering team created this easy-to-use guideline for 3D printing and additive manufacturing technologies—get answers for commonly asked questions specific to designing for PolyJet, SLA, FDM, MJF and SLS. Information includes wall thickness, hole diameter, clearance for assemblies, escape holes, minimum detail, pin diameter, accuracy and standard layer thickness.
Did you know that Fathom offers same-day (PolyJet) and next-day (PolyJet or SLA) services? Learn more about these technologies—as well as FDM, MJF and SLS—on Fathom’s 3D printing and additive manufacturing service page. Need help with technology or material selection? Our in-house experts can help you choose the right technology. Upload files today!