Make the Unmakeable #2: Winner Q&A
From May 4th through June 15th, Fathom partnered with GrabCAD to host the second of three challenges in the 2015 Make the Unmakeable Contest. The competition dares designers and engineers to think differently about how they design and manufacture products by leveraging the unlimited design freedom made possible through additive manufacturing. The judges named Winston Jennings, an experienced Aircraft Maintenance Engineer, the winner of Challenge #2 for his Sphere Wall Mount design. After Challenge #3 launched (deadline is August 31), Fathom asked Jennings to elaborate on his winning design and offer advice for other Make the Unmakeable contestants.
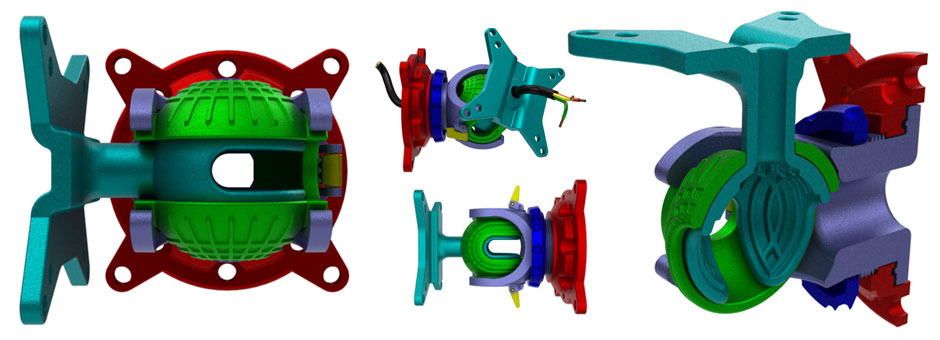
The Sphere Wall Mount utilizes complex geometries to maximize its range of motion and capitalize on the unlimited design freedom of 3D printing — what was the inspiration behind your winning submission?
Jennings: The main idea behind the Sphere Wall Mount was to create a unique design that was fully functional and aesthetically pleasing while also exhibiting complex capabilities that only additive manufacturing could facilitate.
After researching different types of hinges with a focus on those that would benefit most from additive manufacturing, I finally settled on the monitor wall mount. In my opinion, it offers the best combination of complexity, functionality, aesthetics and design freedom for part produced exclusively through additive manufacturing.
Your concept specifically allows for electrical wiring to be routed through the hinge — what are some of the applications you envisioned for this design?
Jennings: This design feature facilitates a wide variety of applications. For example, when mounting small electrical devices such as speakers or lighting fixtures, the Sphere Wall Mount enables a cleaner, more wire-free installation. This takes full advantage of the ability to create intricate cavities and beautiful support geometries; a quality that sets additive manufacturing apart from traditional manufacturing.
I think this concept can be taken even further by mounting other types of devices such as pneumatic actuators that route fluid lines or by adapting it for fiber optics and other special applications. The possibilities are endless.
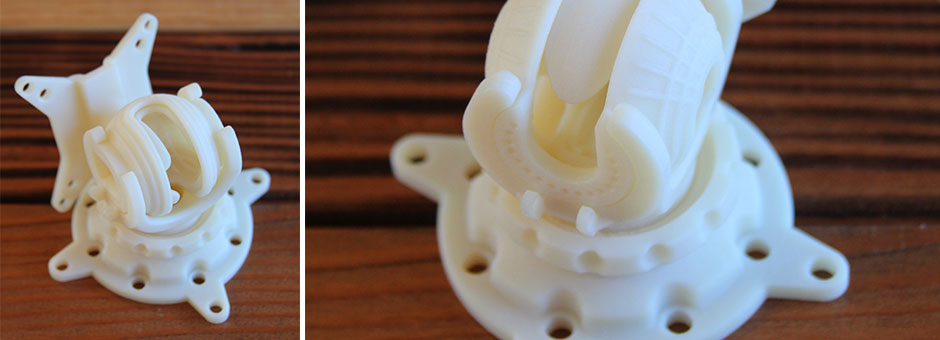
The ability to fabricate assemblies in a single build is a unique characteristic of additive manufacturing — what advantages does this feature offer in the Sphere Wall Mount (image above is a 3D printed prototype of the design in PolyJet)?
Jennings: The ability to boast a “No Assembly Necessary” tagline is a prime advantage—this was something I kept in mind when designing the Sphere Wall Mount. The product is also never in danger of falling apart when loosened since everything is meant to be 3D printed pre-assembled. This quality maximizes reliability, which is crucial for daily usage. The shape also makes this hinge both fun and easy to use, which add to the benefits of the maintenance-free product.
Challenge #3, the last of Fathom’s 2015 Make the Unmakeable Contest, is already in progress— what advice do you have for designers and engineers who plan on submitting designs in this round?
Jennings: From what I’ve learned so far, to come up with a winning design, one must think outside of the box. Traditional manufacturing has certain limitations that additive manufacturing can solve. Think about the limitations of injection molding—undercuts and internal cavities make the part virtually impossible to manufacture using conventional methods.
My advice to others would be to design these limitations into their submissions because these features highlight the strengths of additive manufacturing. Take as much time as you’re allowed to fine-tune the design and make sure they meet the requirements of the challenge at hand.
Once there is a winner for each of the three Make the Unmakeable challenges, those three winners will compete against each other for the grand prize of a uPrint SE — if you were deemed the Make the Unmakeable Champion, how would you use this professional 3D printer?
Jennings: This printer would be a very important tool in my daily life because it would allow me to create hard copies of my digital concepts to test form, fit and function. It would be a tremendous stepping stone for me as a design engineer and bring me closer to establishing a career as an additive manufacturing specialist.
There is also the possibility of developing new concepts for DIY projects. For instance, it would greatly enhance my capacity to teach others how to make retrofits and reverse-engineered parts. Giving back to the community with my ideas and support would be a dream come true.