FDM Materials at Fathom
Three of the Most Used FDM Materials
Fused Deposition Modeling (FDM) is one of the most versatile additive technologies. An appealing aspect of FDM is the large range of real thermoplastic materials available. Typically, a limiting aspect of additive is material selection, but FDM is a consistent exception. Because the process itself is relatively simple, FDM works well with many different materials.
These days, you can find what seems to be any imaginable filament available for use in your printer. A quick web search can find you the options for PLA, PP, PC, PETG, PEEK and more.
Tony Slavik—Applications Engineering Manager.
The options can be staggering if you are comparing it to what you can find for other 3D printing technologies. But just because these materials are available doesn’t necessarily mean they will produce a reliable result. Getting good parts from them can be inconsistent unless the machine is accurately calibrated and the print parameters are clearly defined and exhaustively tested. As a result, some materials, that have been more tested and developed, are more common than others. This subset of materials meets a broad range of application needs and is a reliable go to when choosing a production material. Today we will highlight three of the most used materials at Fathom.
ABS, ASA and Ultem. These three FDM materials make up a large portion of production orders and provide incredibly reliable, accurate and repeatable results.
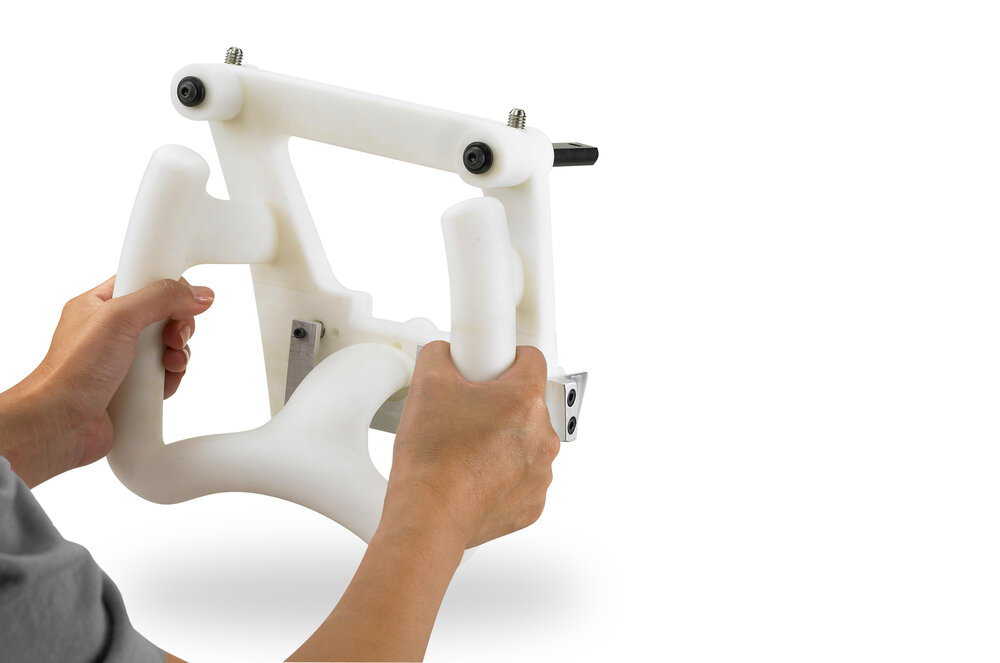
Photo Credit / / Stratasys
ABS is a reliable resin with great name recognition across industries because of its versatility. A “jack of all trades” engineering resin, ABS has been the bell-cow for FDM since the early days. Over the years, the specific blends available have evolved and provided some improvements in stability, color or ESD performance, ensuring that this material is one of the most used FDM materials on the market today.
ABS-M30™ / / Acrylonitrile Butadiene Styrene
-
Versatile material: good for form, fit and functional applications
-
Familiar production material for accurate prototyping
ABS-ESD7™ / / Acrylonitrile Butadiene Styrene – Static Dissipative
-
Makes great assembly tools for electronic and static-sensitive products
-
Widely used for functional prototypes of cases, enclosures and packaging
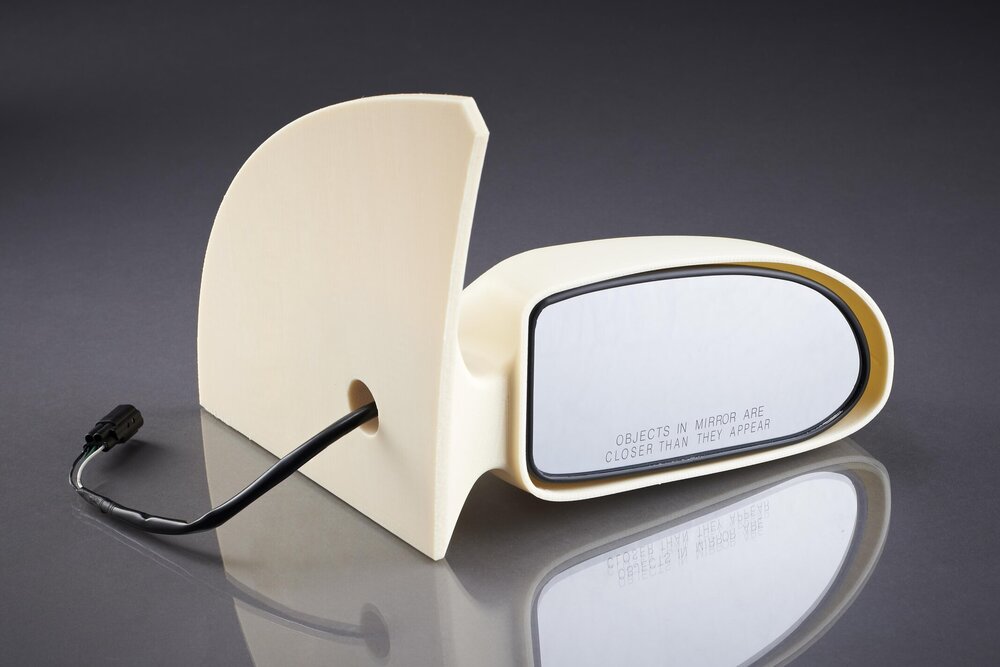
Photo Credit / / Stratasys
Similar to ABS, ASA is being increasingly used as a substitute for ABS. Material properties are similar; tensile strength, heat deflection, impact resistance are all close enough to be negligible. But one reason ASA has become more appealing recently is its UV stability. As additive pushes into more production applications, the demand for performance in harsh environments increases and UV light is pretty rough on ABS. ASA gives an easy solution to that environmental challenge.
ASA / / Acrylonitrile Styrene Acrylate
-
Build UV-stable parts with the best aesthetics of any FDM material
-
Ideal for production parts for outdoor infrastructure and commercial use, outdoor functional prototyping and automotive parts and accessory prototypes
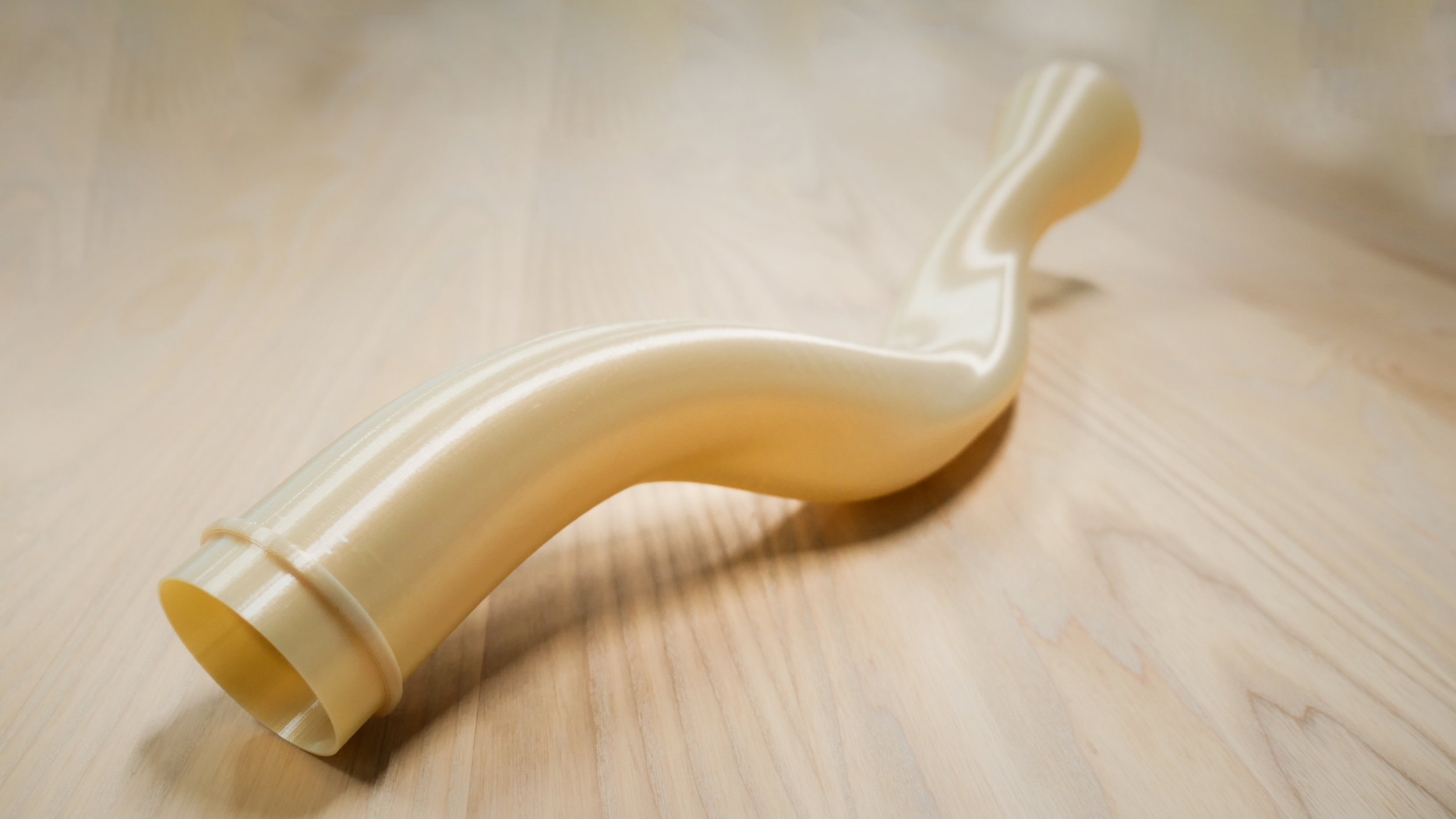
Ultem is one of the most recognizable name brands of plastic in FDM. Two particular blends, Ultem 9085 and Ultem 1010, are extremely high-performance plastics and can be used in some very demanding applications. With high heat deflection, strength and flammability resistance, to name a few, Ultem is a mainstay in the aerospace, medical, automotive and consumer electronics industries. It can carry an FST rating, it can be sterilized for medical applications or it can even be used as a production tooling material for composite tooling.
ULTEM 9085 Resin / / Polyetherimide
-
FST (flame, smoke, toxicity)-certified thermoplastic
-
High heat and chemical resistance; highest flexural strength
-
Ideal for commercial transportation applications such as airplanes, buses, trains and boats
ULTEM™ 1010 Resin / / Polyetherimide
-
Food safety and bio-compatibility certification
-
Highest heat resistance, chemical resistance and tensile strength
-
Outstanding strength and thermal stability