Objet500 Connex3 for Product Design
Vivid color 3D printing is just one of many capabilities available on the Objet500 Connex3. This multi-purpose 3D printing production system can speed up every stage in the product development cycle. From concept modeling to functional prototypes to true-to-life models during the product launch and every step in between. It is important to the Fathom team that we are expert users with all of the 3D printing equipment we sell from our Oakland and Seattle offices. Both of our production centers utilize the PolyJet Technology, among others and we are always looking to get the most out of our 3D printers — just like our machine owning customers. To put this equipment to the test, one of Fathom’s industrial designers created custom electronic enclosure assemblies to be built exclusively on the Connex3 (speakers and headphones). Check out this weeks featured Q&A with Veronica De La Rosa — see what she had to say about the Objet Connex Technology, its industry leading material options and the fun models she created for this interview.
Stratasys launched the Objet500 Connex3 earlier this year (news), the only machine capable of 3D printing brilliantly colored prototypes in a range of multi-material options including rigid, flexible, clear and durable — tell us about your latest project focused on custom electronic enclosures and why you choose to use the Connex3?
Veronica: Currently at Fathom, our design team has been busy designing several consumer electronics; two blue tooth speakers and a set of over the ear headphones. The goal of these projects is to demonstrate to our clients how they can leverage the different technologies and applications offered at Fathom throughout a products development process.
At this stage of our electronics design, we decided to use the Connex3 to test out potential color combinations. The system opens up the possibilities of being creative with color in the electronics market. In our initial renderings of our designs, we settled on very conventional colors (mostly black and various grays). But once we started experimenting with the Connex3 color palette in our render engine, we realized that there were some really great color opportunities to take advantage of — we were really surprised to see how close the 3D printed models resembled the renderings. It’s exciting to see the Connex3 turn the act of 3D printing into something that resembles more of an analog process.
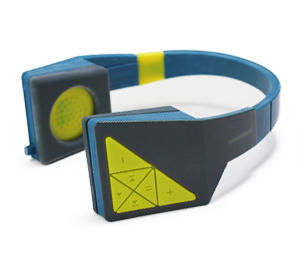
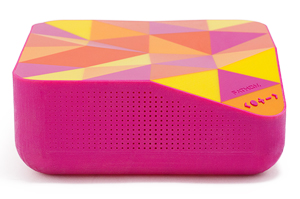
Engineers and designers can leverage the Connex3 throughout the entire product development cycle, from proof of concept and abstract models to functional prototypes and fully finished presentation models — what does this comprehensive modeling solution mean to engineers and industrial designers?
Veronica: The Connex3 is a really comprehensive tool for designers and engineers to use throughout the entire product development cycle. In the initial conceptual phase, designers and engineers can use it to print out monochromatic models to focus on evaluation of form, proportion and ergonomics. Further in the design process, designers can print out more diagrammatic models where parts in the model can be color coded to represent different information. For example, structural analysis can be printed directly onto models informing designers of potential structural failures.
As discussed previously, printing on the Connex3 can produce final color models much faster than painting and finishing prints. For marketing purposes, final CAD files can be printed and undergo model finishing for more realistic looking models. With the ability to print Digital ABS with over-molding, designers can create models that not only test the look of their designs but also the functionality. These are just a few examples of how the Connex3 can help designers learn more from their design processes to create better products faster.
Just as 3D printing sped up the prototyping process for engineers and industrial designers, time to market is even faster now that colors are available to creative teams so early in the design process — what does this mean to engineers and industrial designers?
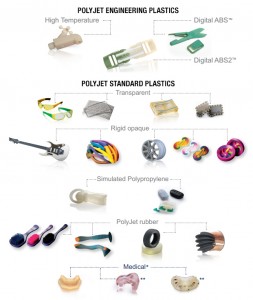
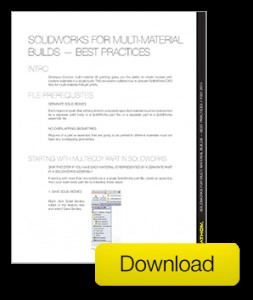
Veronica: Giving designers access to color so early in the design process can really open doors to experimentation and innovation. Models can be printed in different colors and presented to focus groups to validate design decisions early in the process.
In addition, the Connex 3 can also simulate different colored materials. For example, models can be printed in different colored durometers simulating colored over-molds. Being that the Connex3 is the only printer to offer translucent color capability, designers can experiment with light transmittance and create different layering and lighting effects.
When creating files for this type of application, how does the 3D CAD modeling process vary compared to 3D printing on other Stratasys systems? Tell us a few tips and tricks, too.
Veronica: I primarily work in Rhino and use layers to organize the geometries in my files. During the modeling process, I usually create layers based on my CADing process. I am not typically thinking of materials during this stage. So, when it comes time to print my files, I save out a version just for printing and create layers for each of the colors I want to use.
Then, I move all the parts of the same material in the model to their respective layers. I do this so I can easily select the same material parts within the model. After that, I export all the same colored objects at the same time as one STL. I repeat this for all the colors in my model. This way when the STLs are imported into Objet Studio, our production engineers can easily assign a color to the specified STL group that I exported. Our team created a white paper on exporting CAD files for multi-material 3D printing, I recommend checking that out (download white paper).