SF Design Week / / Fathom Designer
Fathom Industrial Designer Ava DeCapri is up for any design challenge, having worked on various projects spanning industries from consumer electronics to automotive to medical. DeCapri has worked with companies large and small and led Fathom’s contribution to the Enable Community Foundation, a nonprofit organization that brings 3D printed prosthetics to those in need. For this years San Francisco Design Week from June 14th to the 20th, DeCapri will be participating as a panelist during a session on products made in the East Bay region. We checked in with her before the event—learn more about what influences DeCapri, her most memorable project and what she wants you to know about the impact 3D printing is having on todays product development process.
What influences you as an industrial designer?
DeCapri— I am a futurist and a dreamer and I am always inspired by the things around me to make and create, but the one thing that leaps to the forefront for inspiring me is technology. One of the reasons I joined the design team at Fathom was to have unlimited access to 3D printing and additive manufacturing technologies. To be able to play and experiment with the possibilities of this new medium. I am still being pushed by the technology to discover new ways of thinking, designing and manufacturing. 3D printing is just one extreme example of technology that inspires me to create in new ways, but the complex process of learning about a manufacturing process, both new and traditional forms of technology, always spawns ideas about new ways of making as you build upon your knowledge set. Part of the magic is that you are always building your database of technology and material options and you will gain a unique perspective and skill as you seek new ones, as well as processes. If I could learn about new materials and technologies for the rest of my life, I would be a happy designer.
I do have to mention that a big inspiration for me is fine art. While I value studying the work of the designers and engineers I admire, I find it more liberating to look to other mediums for inspiration. I discover that the results can be unexpected and I can avoid being derivative of products or designs seen in our field already. One artist I truly admire and return to often is Alexander Calder who had a similar wonderment for materials and traversed many mediums.
What project has been most meaningful to you during your career at Fathom?
DeCapri—I am most proud of the work we did with the Enable community foundation, designing and building custom low-cost prosthetic limbs for young kids. It sounds as fun and challenging as it was! What made this endeavor successful was that we dedicated a lot of time to really digging in deep to understand their world and the challenges that were ahead of us. We learned through experimentation and failure which carried us through three separate projects for two young kids. We also had a huge community that had built up research into this new space to work from, which is an unusual resource to have in design.
Designing things on an open source platform opened a new part of my brain that allowed me to envision new ways of sharing and manufacturing products beyond prosthetics. What made this project most significant to me was the effect that our team had on these young kids lives. Not only were they empowered by their new tools, mostly emotionally, but they were learning about design and engineering in a way that was very immediate and relevant. One of our participants in the prosthetic program, David, even contributed to building his arm using Autodesk’s TinkerCAD! Its inspiring to see the next generation embrace technology and use it to their advantage.
What impact does your work have on product development today that youre most excited about?
DeCapri—I am most excited about the shift in the manufacturing space, due to advances in technology, that allow for smaller and more experimental production runs. This allows for innovation in process and materials when designers can experiment and prototype on the same machines that they will use to manufacture. For example, the open source project, Precious Plastic, has put designs online for machines that process and reshape recycled plastic. In the 3D printing world, this is direct digital manufacturing (DDM) which means producing your final parts on a 3D printer or additive manufacturing system.
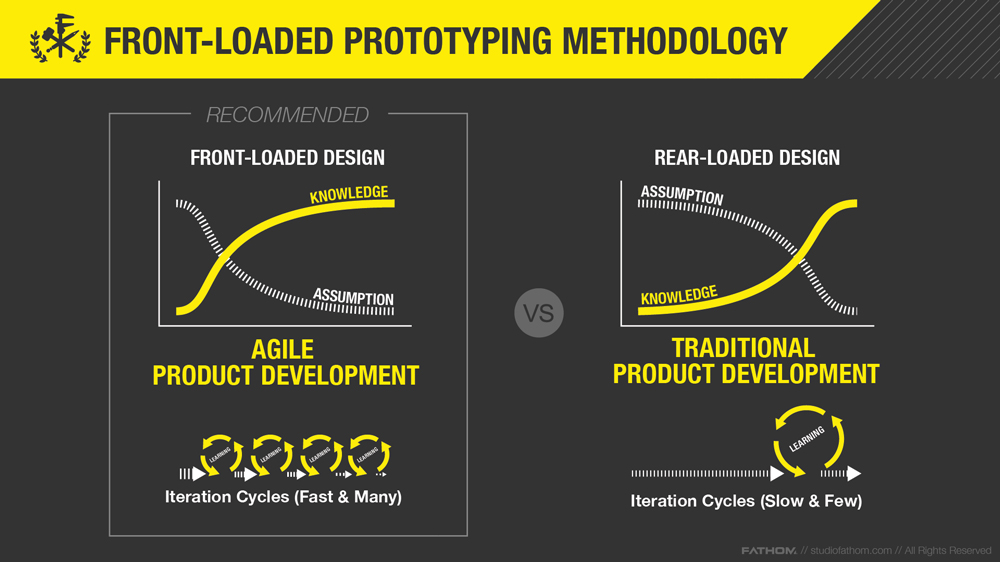
Image Description // By taking a “front-loaded” approach during the prototype phase—engaging in many iteration cycles—teams can increase knowledge and decrease assumptions earlier in the concept development process when it is less costly to make changes.
What challenge do you face the most in the advanced manufacturing space?
DeCapri—The biggest challenge we face as a team is furthering the education and adoption of designing for additive manufacturing (DFAM) and enterprise 3D printing. There is a lot of hype and misconception about what 3D printing is and what the technology is capable of and there is a big difference between consumer and enterprise systems. Most people are familiar with consumer 3D printers and often project those expectations onto enterprise 3D printing, which has drastically different material, capability and build volume options—just to name a few.
Enterprise 3D printing has already entered the manufacturing realm. While it can substitute legacy manufacturing processes we are familiar with, we can achieve its full potential when we design for it—3D printing opens up a whole new world of possibilities in form, material properties and new manufacturing processes such as rapid tooling and greater part complexity that were not possible before. It requires a shift in thinking and understanding of the process, but is worthwhile and results in many innovations.
If you could change anything about your process, what would it be?
DeCapri—Sometimes I realize Im not taking full advantage of the iterative process that 3D printing affords.With 3D printing, you can iterate with physical prototypes and see for yourself how things come together instead of relying on a computer rendering. With technology that allows you to iterate quickly in real materials, you are able to “front-load” your design process (see below), creating much more progress and understanding early on in your design process which allows for less assumptions and better products at the end of the process. A colleague of mine once prototyped 20 designs for a prosthetic limb extension in a single day! It was a small part, but this allowed us to take what could have been a month long exploration and get results in a day.
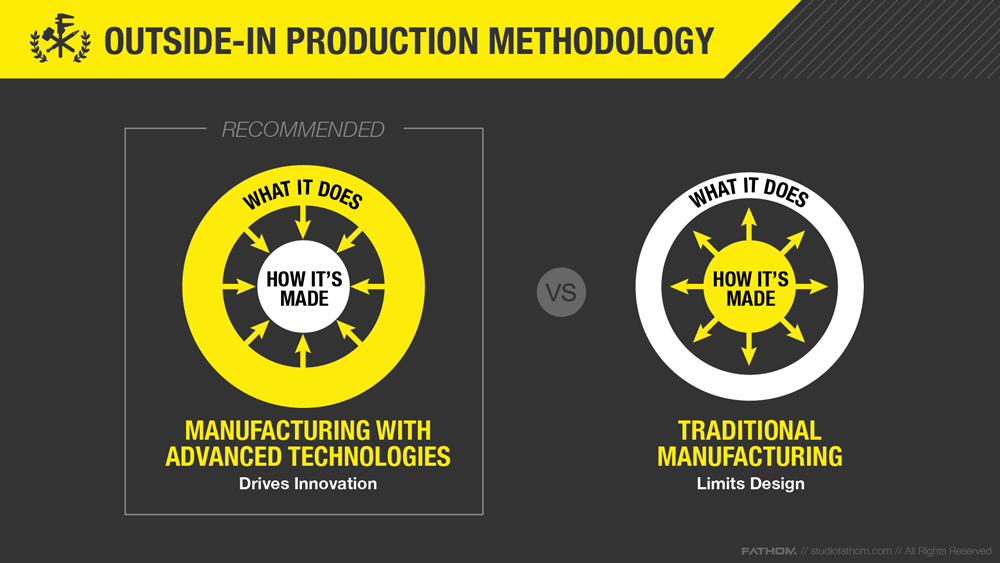
Image Description // By focusing on how a product should function rather than how it’s made, companies can drive greater innovation and push the limits of manufacturing—whether manufactured traditionally, additively or a hybrid of both, Fathom promotes an “outside-in” approach to generate better products with the greatest functionality.
If you could emphasize one aspect of your process with clients, what would it be?
DeCapri—Be open to discussion because we can learn from each other. Our team loves learning from our clients and it is always better to start a project with a cultivated environment of trust and learning than to come to it with strict guidelines or assumptions on how something should be made. Our team promotes an outside-in approach because greater innovation is realized when everyone is focused on how a product will function, not how it will be made. From there, our experts help companies figure out what technologies, materials and processes will bring their concept to life. Oftentimes at Fathom, advanced technologies like 3D printing are used with traditional methods to solve highly complex problems in ways and at speeds, not previously possible. The result is significant when those differing strengths and weaknesses of advanced and traditional technologies are used to augment each other. Hybridization of manufacturing processes is an overarching strategy at Fathom for achieving the greatest efficiencies and innovations. Its exciting to be a part of that journey with our customers. At Fathom, we like to take on projects that are a challenge for other manufacturers and this requires a mutual trust and respect from each other. We don’t know everything, but we are sure eager to learn and we always make it happen for customers!
Check out more information on SF Design Week at the event website.