On-Demand Inventory with DDM
Additive manufacturing has transformed the landscape of production, better enabling business agility in manufacturing with additional degrees of flexibility in supply chain management. In this featured blog post, Innovation Program Manager Phil Stob talks about the trends and shifts hes seen during his career, from working with Toyota in the 1990s to overseeing many of Fathom’s cutting-edge projects with innovative customers. Stob started his career in quality control at Toyota and later moved into product development for companies like IDEO. Throughout his manufacturing engineering experience, hes worked hands-on with designers and engineers to bring products to market using proven production methods such as tooling and injection molding. As the Innovation Program Manager at Fathom, he leads a team of experts who are blending additive manufacturing with traditional manufacturing methods.
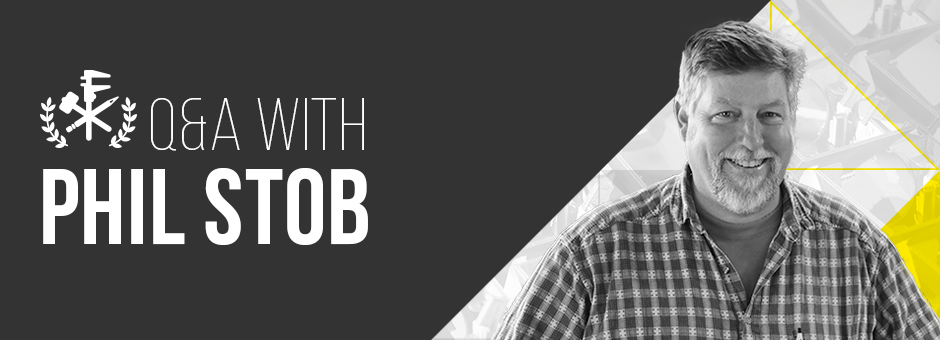
How has additive transformed manufacturing throughout your career in product realization?
Stob—I have been involved with product development and new product introduction for the past 25 years. What 3D printing has done for me and the industry, is reduce the time to prove out concepts and finalize designs, along with a higher confidence of success. My role has often been to get all the stakeholders together for agreement and with 3D printing, it all become a bit easier. Engineers can confirm for fit and function, Industrial Designers can confirm the feel, appearance and weight of the unit and C-level members can get a much clearer view of what the project is, including its issues and challenges. Changes to the design can be done overnight and reconfirmed the next day, rather than taking two to three weeks. Fast projects can go quicker and tricky design issues can get resolved much faster. One added benefit is when running a pilot build, a corrected 3D printed part can be run overnight, compared with sending 1,200 problem parts for rework in the machine shop. In production, parts always need a bit of tweaking or tuning and 3D printing makes all of this much more feasible, with no wasted inventory.
Compared to traditional injection molding, how has direct digital manufacturing (DDM) changed production timelines? For an order of say, 200 parts, how do considerations of time and cost compare between additive manufacturing and injection molding?
Stob—Making 200 parts with additive manufacturing should take a day or two, while a molding option, even with our fastest tooling options, will take five business days to three weeks, depending on the geometry of the parts. And even if after you make the first 50 parts and want changes, it’s possible to start making new parts today with DDM, while the injection molded process may take several weeks to make the changes and confirm.
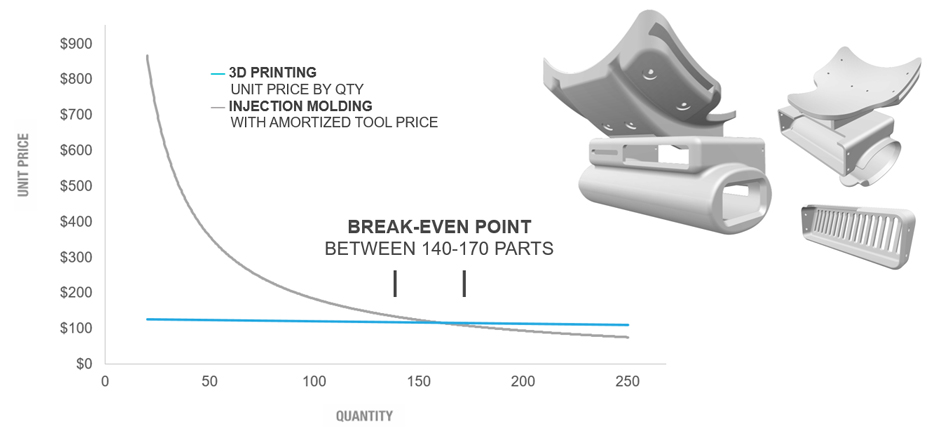
Costs vary according to the individual part, of course, but is there a rough number of parts you would estimate as the minimum amount needed to mandate tooling for an average company?
Stob—It’s a bit difficult to answer this with a hard and fast number, as the geometry of the part and functional requirements come into play. Some parts are better off being made using FDM or some other 3D printing method because of the part geometry. For injection molding, undercuts and holes require additional tooling time and increase cost and some parts just simply cannot be made with injection molding. The best way to showcase the potential savings here is through a use case. VRstudios, a growing virtual reality company based in Washington state, found that the break-even point between injection molding and 3D printing for the battery enclosure in their VRcade headset was between 140-170 parts.
By opting for a tool-less manufacturing approach, VRstudios lowered production costs and achieved a greater degree of agility in filling orders and managing inventory. The team is also not locked into one design and can 3D print the latest revision as needed without holding inventory on an outdated design. Using additive technologies to produce production parts is becoming more common as designers and engineers familiarize themselves with designing for additive manufacturing (DFAM).
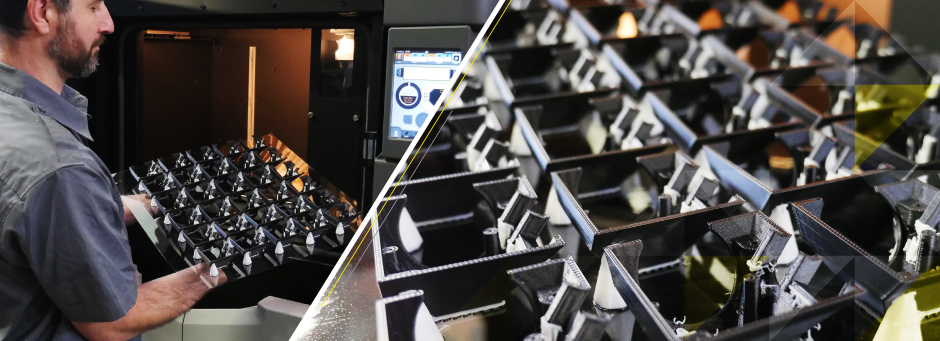
How does DDM change the way a company handles inventory? Are there advantages to a DDM approach from a logistics or warehousing standpoint?
Stob—The full cost of a part is not just the purchase price. There are costs associated with shipping, handling, inventory control systems, material handling systems and staff, warehouses, wastage and shrinkage, inventory damage, obsolescence from design changes, packaging and many others. With DDM, complexity is basically free and combining parts and making complex geometries will start to make assemblies cheaper and more durable. The savings on assembly costs and fit issues make DDM a competitive option. If properly accounted for, a DDM part could cost twice as much as a regular production part to create, but still be far cheaper in the long run because of the avoidance of many other associated production and inventory costs.
In a highly developed Just-In-Time (JIT) production system, all of the inventory is directly delivered to line side. The ideal is always to make the shortest supply chain possible and many manufacturers have put suppliers in the same building or nearby. With DDM, its very feasible to put the machines in the factory and potentially next to the point of use. Inventory levels can be kept very low and production can become essentially on-demand, freeing up valuable supply chain management resources. Ordering today for what is needed today becomes much more realistic. Long range forecasting and changes in demand become smaller issues with on-demand production.
How do you expect production to shift in the next decade? Do you think we will see a geographic shift?
Stob—With DDM, whether a plant buys a machine or just a service, all you really need is adequate power and access to a shipping service. I think that smaller scale manufacturing and decentralized production will continue to increase in the near future. I think that there will be many more small companies in places where people want to live, without the need for a larger manufacturing infrastructure to make products.
Do you foresee a rise of “advanced manufacturing” jobs since more companies are employing DDM strategies?
Stob—Certainly. DDM requires a level of technical expertise to work with 3D CAD and an ability to design for additive manufacturing (DFAM). In modern manufacturing, familiarity with additive is a must from a competitive standpoint. The companies that can tie together all of the benefits of DDM into their products, along with the scaled advantages of mass production, will see the greatest success. Additive hardware, software, materials and processes will certainly drive a shift, but the longstanding benefits of traditional manufacturing arent going away anytime soon. Hybridized production is the present and the future.
Start a conversation with Fathom today! Fill out the form on the right and we will be in touch with you shortly. Fathom takes a technology-agnostic approach to solving your application challenges, so we offer a comprehensive list of manufacturing services to support all of your prototyping and production part needs—3D printing, additive manufacturing, CNC machining, urethane casting, tooling, injection molding, R&D and concept development (industrial and mechanical engineering support). Learn more from speaking with an account manager at Fathom.