3D Printing Scaled Industrial Assemblies
High-quality models that perfectly imitate a real product can generate greater engagement than just a photo or illustration on display—but traditional production processes can be costly, lengthy and involved. Taking a tool-less manufacturing approach by way of additive technologies and materials, teams can quickly fabricate realistic looking parts with the finest features and details. Fathom uses these techniques to bring companies from CAD files to finished parts faster and more efficiently. Always looking for creative ways to showcase his company’s industry-leading machinery, American Piledriving Equipment President Dan Collins approached Fathom with a challenging 3D printing concept. For an upcoming slate of industry technology shows, Collins wanted to show the world’s largest pile driver, APE’s “DodecaKong,” but one that would actually fit inside show halls and convention centers.
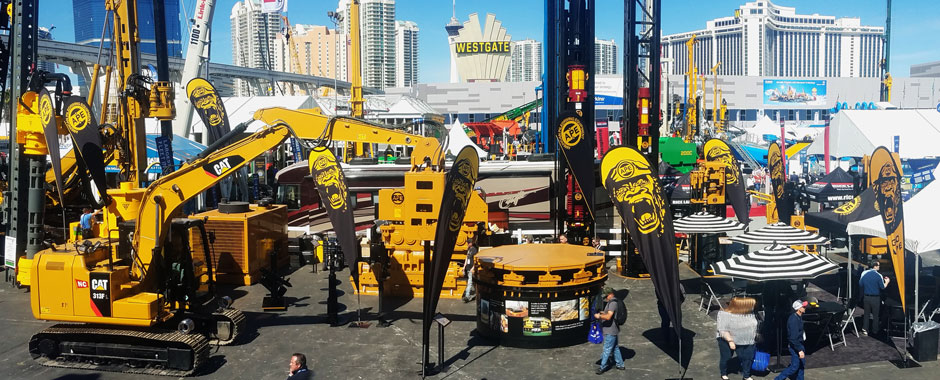
With a diameter of nearly 100 feet and a full weight surpassing 600 metric tons, the record size driver is more than slightly difficult to maneuver. Hoping to achieve a model with identical appearance to the DodecaKong pile driver, Collins looked to Fathom for a lightweight show model that would retain the precise detail customer would expect to see during installation (actual pile driver pictured above).
Fathom Account Manager Ryan Brand and the production team were up to the challenge. Fully 3D printed on a Fortus 900mc and other Stratasys additive manufacturing equipment, the 10-foot wide assembly of parts required more than 600 hours of FDM-based 3D printing time and was completed in less than two weeks.
In this featured Q&A, learn more about APE’s DodecaKong show model from a number of project stakeholders, including Collins, Brand and Fathom Production Manager Tony Slavik.
Describe your show model project and the challenges that it posed.
American Piledriving Equipment President Dan Collins—We were modeling very large construction machinery and needed to stick to a 1:10 scale. The various parts of the assembly needed to be a bit more than 13 inches tall and 18 inches wide, which was too big for most 3D printers.
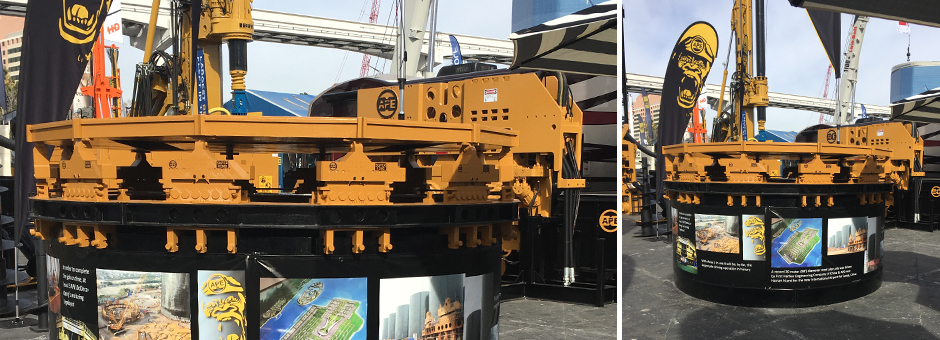
What aesthetic qualities were key to the show model? What level of accuracy was needed? What were the allowances?
Fathom Production Manager Tony Slavik—With time and size as major hurdles, our production team leveraged Fathom’s FDM-based Fortus 900mc to fabricate the large parts (build tray of 36 x 24 x 36 in). We provided design guidance before the build and changes were made to the 3D CAD files to ensure the highest quality parts while still meeting accuracy requirements. By 3D printing these parts with sparse fill and .013 inch layer thickness, we could fill the large order within the two-week window—optimizing part orientation, customizing tool paths and choosing the right fill density are all critical considerations for achieving the desired weight, strength and surface finish. In all, the project took around 600 hours of print time (10-foot wide show model pictured above).
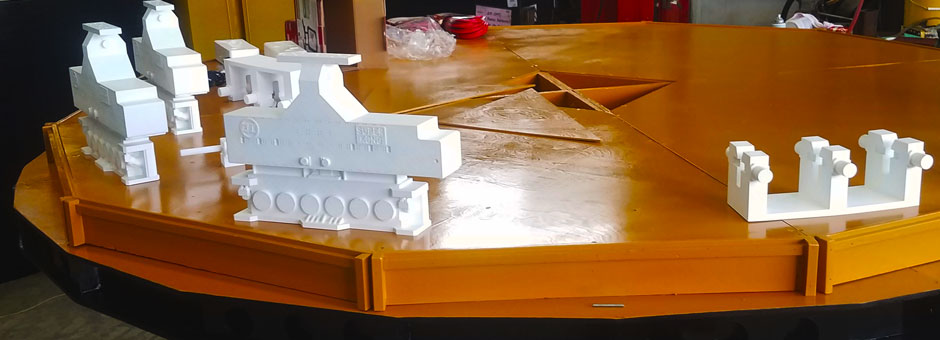
Why was 3D printing chosen rather than urethane casting or another production method?
Slavik—The models were scaled-down versions of large industrial assemblies. Any traditional manufacturing method would have required complex assemblies and high tooling costs to capture the intricate details. With 3D printing, we were able to skip a lengthy DFM stage that would have been necessary if we were to use CNC machining, urethane casting or molding to produce any of the parts. We would have had to break it down into components, simplify and merge parts to reduce costs and design tooling. Our initial conservative estimate for this design step was that it would take 4-5 days. With 3D printing, we were able to take the model as delivered by the customer, with all of it’s intricacies and undercuts and move directly to production.
Fathom Account Manager Ryan Brand—3D printing was the only viable option given the turnaround time. While PolyJet-based 3D printing could have produced solid parts faster, FDM allowed us to 3D print the large parts in sparse fill, conserving both material and time to fit APEs project schedule and budget.
What do you expect in working with an advanced manufacturer?
Collins—Quality products done on time, every time. Good scheduling and keeping commitments is what keeps our customers coming back to us and what keeps us coming back to suppliers like Fathom.
What requirements were most important for the project? Did Fathom employees do anything extra to help ensure the success of the order?
Collins—Yes, they were able to give us suggestions on our model design in order to keep the project within our budget and timeline. Ryan was very easy to work with!
How did Fathom ensure the success of this project?
Brand—Ongoing communication is the key to any successful project and this one was no exception. We clearly set expectations with the part finish quality and lead time so APE could plan accordingly with their finishing and assembly team and coordinate with the freight company responsible for shipping this installation to Las Vegas in time for their trade show.
To learn more about DodecaKong, visit the American Piledriving Equipment website!
To start a conversation about a project or discuss a quote for 3D printing, CNC machining, urethane casting, rapid tooling, injection molding or R&D contract services, send us a request for quote. Fathom is also an authorized partner of Stratasys. Get a quote for a professional 3D printer today!