Featured Part / / Annual Fathomer Awards
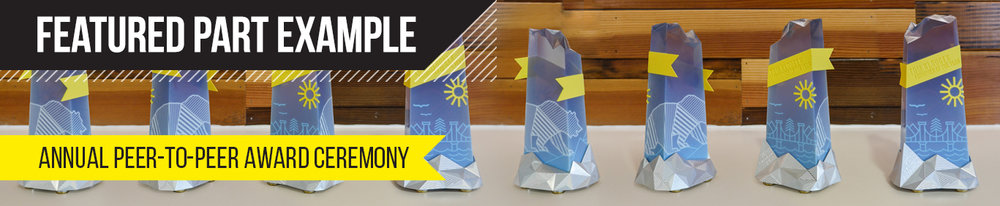
Making Fathom’s Generatively Designed 3D Printed Employee Awards
Each year, the creative minds on Fathom’s engineering and engineering team make unique trophies for the employee nominated award ceremony during the Fathom’s annual Kick-Off event at the beginning of the year. Fathomers take time during December to acknowledge each other’s contributions made throughout the year. Those with the most nominations per category receive a custom trophy during the kick-off. This year, they worked with both our additive manufacturing and CNC machining production teams.
Featured Method Used // Advanced Slicer & Texture Mapping
Featured Software Used // Adobe Photoshop CC
Additive Technology Used // Full-Color PolyJet & Dyed SLS
Subtractive Technology Used // 5-Axis CNC Machining
Fathom Teams // Engineering/Design + Additive Manufacturing + CNC Machining
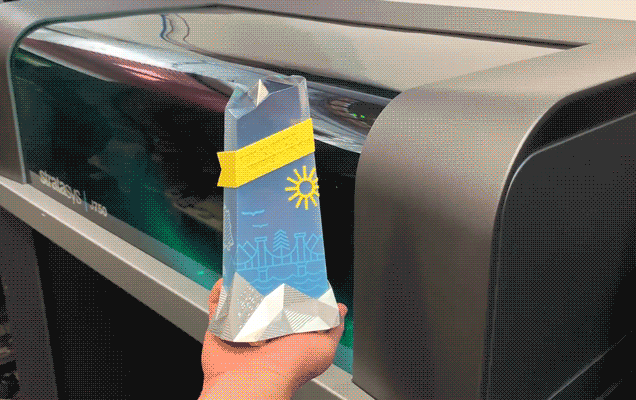
The Part // A trophy for each Fathom award winner inspired by the company’s 2018 theme of “CONNECT.”
The Project // The project highlights the advanced slicing capabilities of the PolyJet-based J750. 3D printing VRML files with full color graphics mapped to the surface of the part was managed with the advanced slicer add-in for the J750 PolyJet-based 3D printer. To fabricate the part, a graphic was generated in Adobe illustrator that corresponded with the faces of the part. The meshed part was then brought into Adobe Photoshop where the surface of the part was unwrapped to create a flattened or 2D, version of the 3D part. The graphics are then applied to the 2D unwrapped map, this informs where the graphics will be placed on the 3D version. In this method of unwrapping, applying graphics and rewrapping the graphics back on to the part, we can achieve seamless graphic artwork on the surface of a 3D body that would otherwise be difficult to produce.
The metal base was designed to be milled on 5-axis CNC machining equipment. Since the form has shallow cosmetic surfaces, the base would be impossible to be created on the 3-axis machine. The bottom was machined first with the feet of the trophy being the mounting points for the 5-axis machine holding. With this method, creating detail on the bottom of the trophy was accomplished while simultaneously creating features to easily fixture the part to the 5-axis machine. The machining design was a collaboration between the designer and the machinist, with a lot of the aesthetic detail being added to the part in the toolpath design.
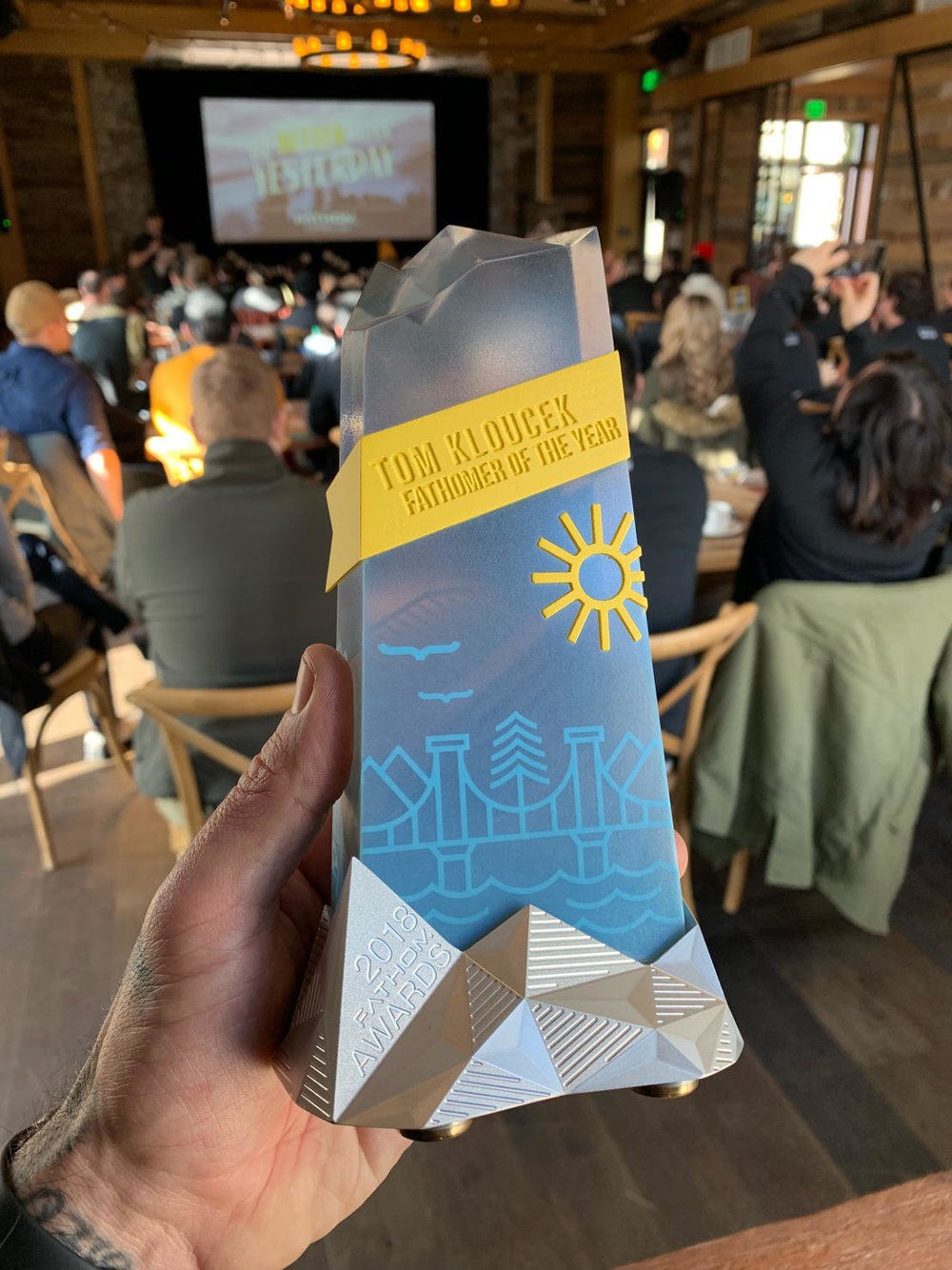
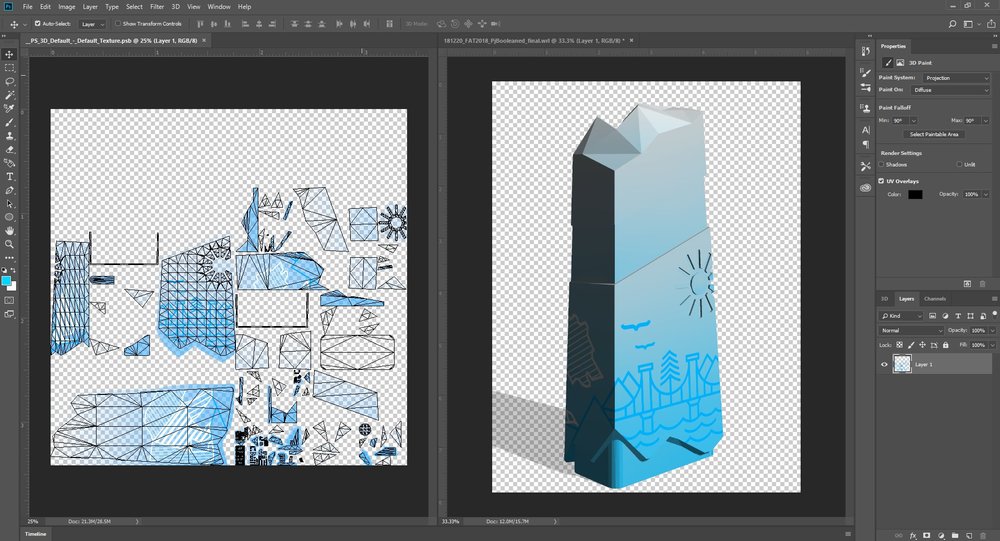

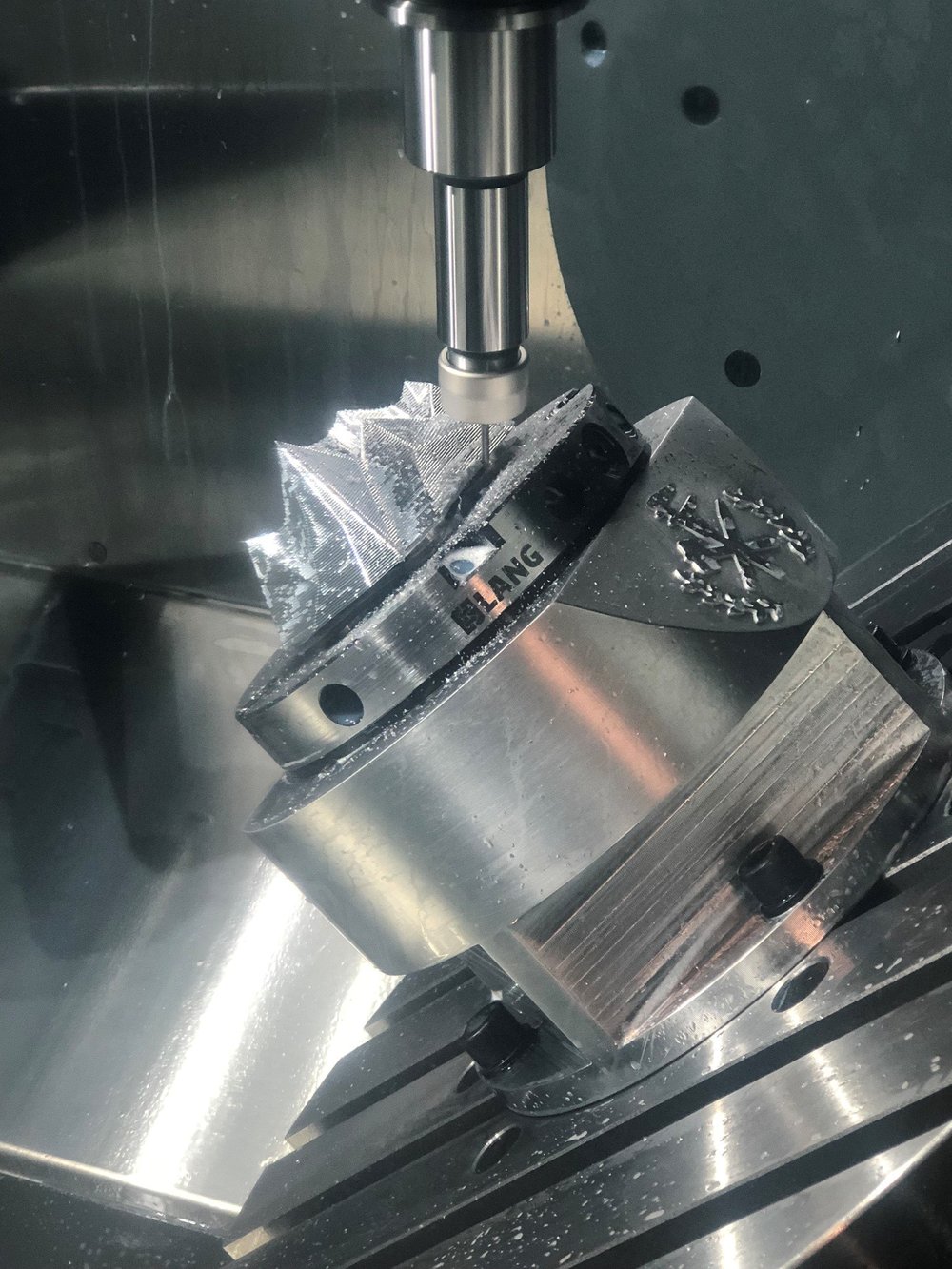
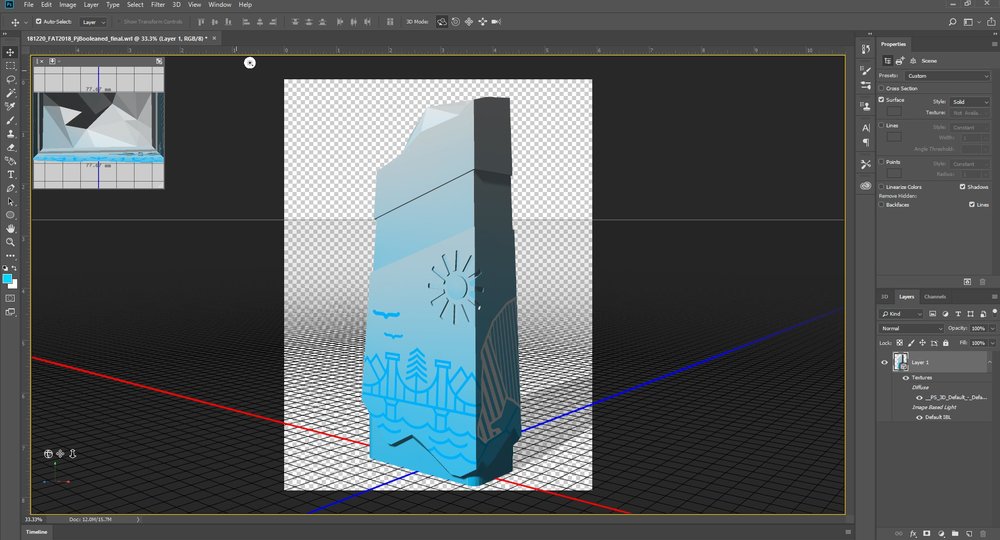
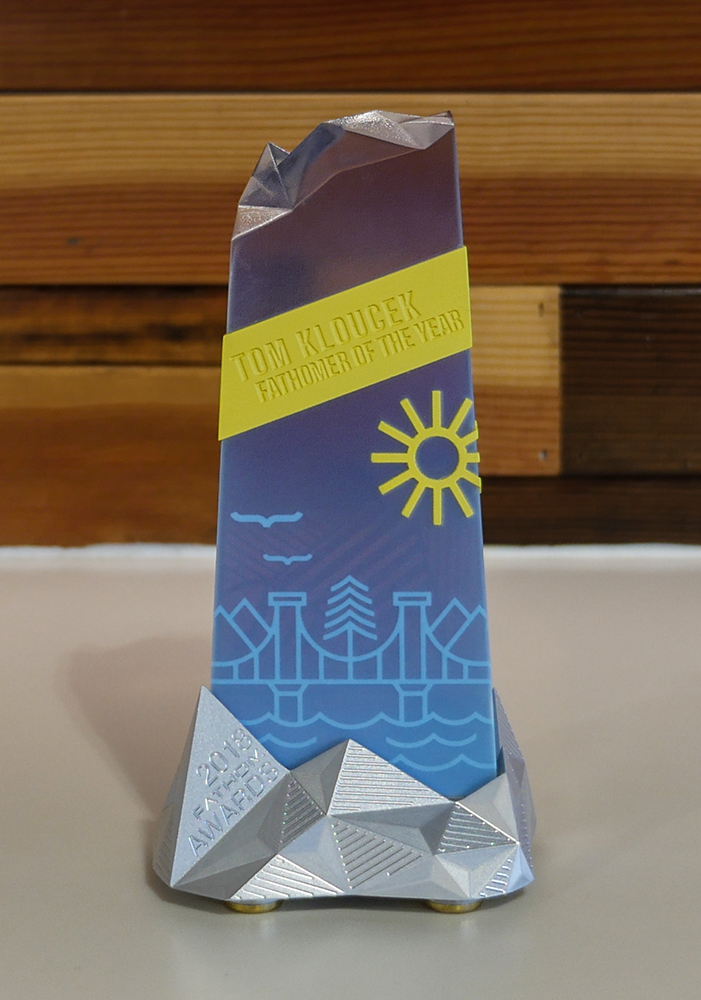
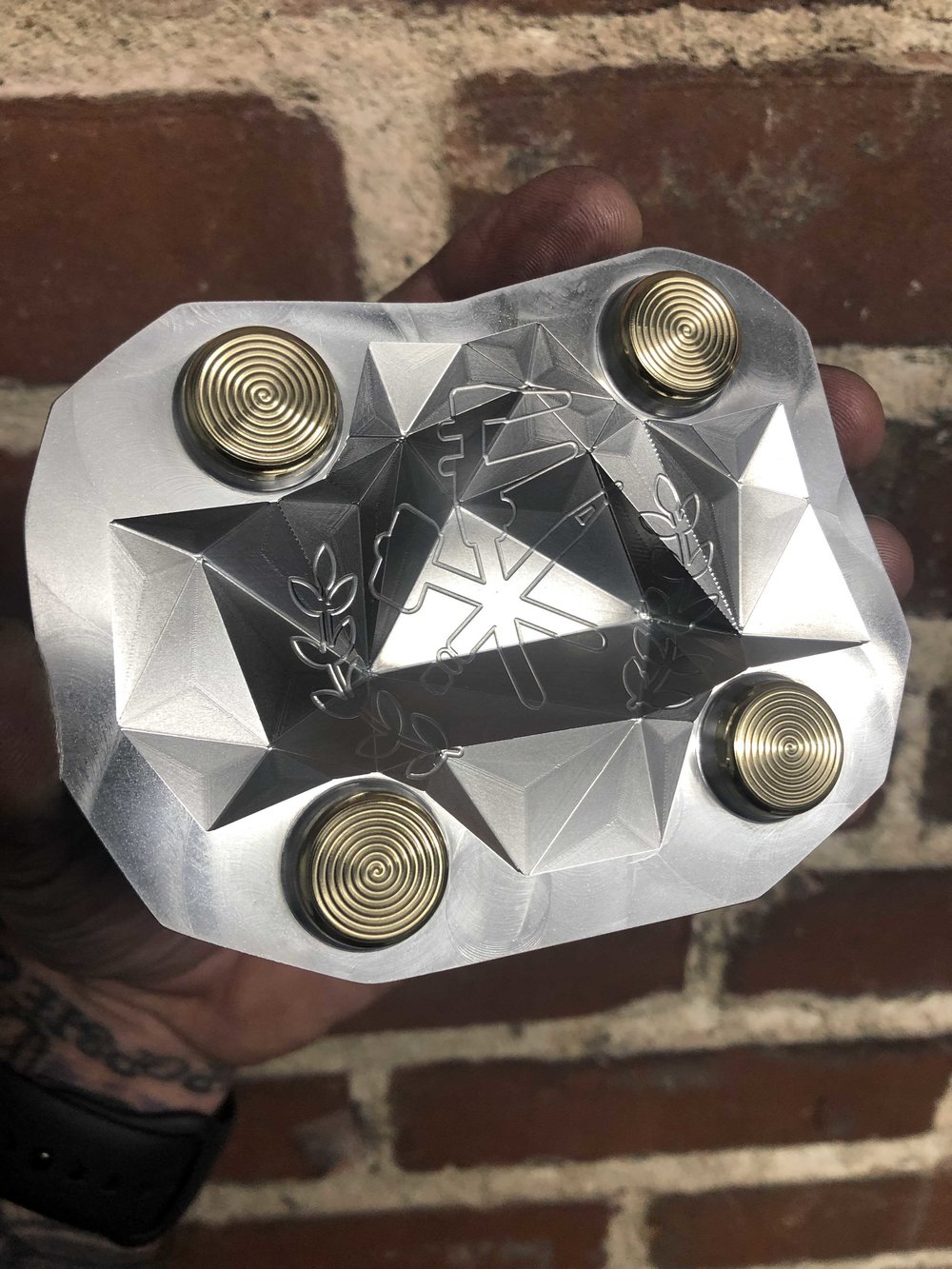
Did you know that Fathom offers a Design for Additive Manufacturing (DFAM) training program that highlights effective approach to design & manufacturing from an additive technology perspective? Click thru to learn more about this custom curriculum focused on the practical application of today’s technologies for modern product development.
Learn more about Fathom’s engineering & design help—start a conversation today!