From Prototype to Production
Startups Experience Rapid Tooling and Injection Molding Facility for the First Time
Rapid prototyping techniques like 3D printing ignited a renaissance in hardware and encouraged new entrepreneurs to innovate with connected devices. This same convenience in prototyping can mask the complexity and scale of commercial manufacturing to an entrepreneur that has never shipped a consumer product. Helping startups bridge the gap from prototype to production is part of our mission at Fathom.
“The sheer scale and size of the tools and the presses, creates a sense of wonder for someone who hasnt been at an injection molding facility before, said Ben Bradley, SmartQuote Specialist at Fathom. Its extremely important for these startups to understand the process and see it firsthand.
Oftentimes startups get comfortable with using 3D printing and other additive manufacturing technologies to develop prototypes throughout the iterative process, but there is much to consider when going from that final design to production.
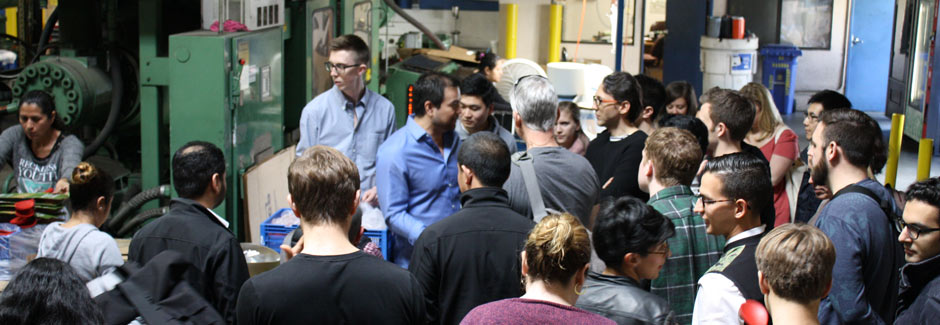
Oakland-based advanced manufacturer Fathom and hardware startup accelerator Highway1 strive to help young hardware companies succeed in making it to scaled production and a large part of that process is sharing knowledge of the best ways to build the bridge from prototyping.
“As we progress the design of our product to something that’s commercially viable, it was great to hear from the professionals in the room about what typical missteps are made as startups approach the manufacturing transfer phase,” said Tim Ahong, CTO of Sensassure. “Learning about both how much work is required after our design phase is complete—much more than we thought—and how to most efficiently bridge to production to complete that and to have the most successful commercialization process possible was extremely valuable.”
Fathom and Highway1 frequently facilitate manufacturing floor tours like this one so designers, engineers and creative thinkers-alike can have a first-hand look at what goes into the tooling and injection molding process.
For most, their first walk through inspires a feeling of awe. Seeing actual injection molded parts come through machines is key to realizing the pace of production. This experience opens people up to the many realities that come with taking their design to production and the risks involved if their design is not properly prepared for manufacturing at this scale.
This collaboration between Fathom and Highway1 provides a great opportunity for startups because they get to see real world examples of the product development cycle; from proof of concept models to actual production, said Preeya Singh, Territory Manager at Fathom. It is important that these groups start conversations early on so companies like Fathom can help mitigate a startups manufacturing risks, reduce time to market and achieve a seamless transition from prototype to finished part.
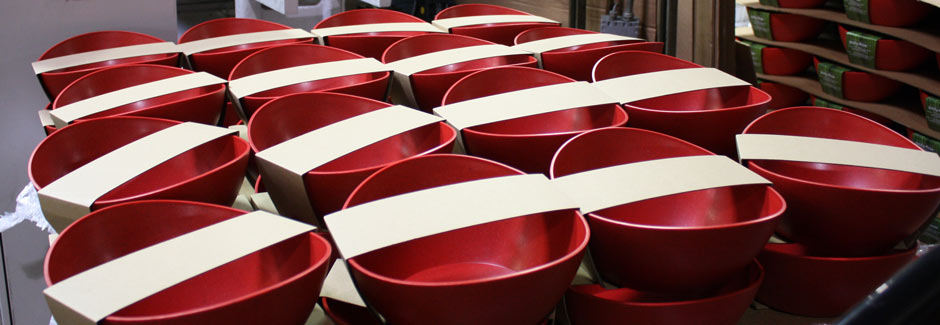
To learn more about Fathom’s advanced prototype fabrication and bridge-to-production services (additive technologies, CNC machining, urethane casting, rapid tooling and injection molding), talk to an account manager (use the form on the right). For a look at how the San Francisco Bay Area startup Doblet went from 3D printed prototypes to production parts, check out an exclusive interview with Co-Founder Jeff Chang.
For more about Highway1 and how they are accelerating the startup trajectory, check out the Highway1 home page.